Freezer Troubleshooting
Troubled by freezer failure? PHP editor Xiaoxin brings you a freezer troubleshooting guide to solve common problems for you. From simple checks to complex repairs, this article will guide you step-by-step in diagnosing the problem and getting your freezer back up and running. Read below to learn how to fix problems like overheating in the refrigerator, not working ice machine, excessive frost, and more, and get back to enjoying the thrill of ice.
1. Freezer troubleshooting
How to effectively troubleshoot freezers
It is very common to use freezers at home, however, sometimes there will be some malfunctions in the freezer. When a freezer malfunctions, how should we effectively troubleshoot these problems? This article will introduce some common freezer failures and provide corresponding troubleshooting methods, hoping to help everyone.
Common freezer failures
The freezer cannot cool. The freezer is leaking. The freezer is too noisy. The freezer door is not tightly sealed. The freezer cannot be started. At the same time, you can also check whether the compressor of the freezer is working properly and whether there is fluorine leakage, etc. If there are no problems with the above, it may be that the freezer is low on refrigerant, and professionals are required to add refrigerant. Freezer leakingFreezer leaking may be because the drainage hole of the freezer is blocked, preventing water from draining out normally. At this point, you can use a hose to clear the clogged drain hole. If the problem persists, it may be caused by the aging of the sealing strip of the freezer, and the sealing strip needs to be replaced in time. Freezer is too noisyIf your freezer is too noisy, it may be because the compressor of the freezer is working abnormally. You can check whether the compressor is normal. If problems are found, the compressor needs to be replaced in time. In addition, unstable placement of the freezer can also lead to excessive noise, requiring the freezer to be repositioned. The freezer door is not sealed tightlyThe freezer door is not sealed tightly, which will cause the cold air to leak out, thus affecting the cooling effect of the freezer. You can apply soapy water on the sealing strip to see if there are bubbles. If there are, the sealing strip needs to be replaced. Timely replacement of sealing strips can improve the cooling effect of the freezer and save energy. The freezer cannot be startedWhen the freezer cannot be started, you should first check whether the power of the freezer is turned on normally. You can also check to see if the fuse is blown. If so, the fuse needs to be replaced. In addition, you can also check whether the control panel of the freezer is faulty and needs to be repaired or replaced. In general, freezer failures are very common, but as long as we can discover the problem in time and take effective measures to solve it, we can eliminate freezer failures and keep the freezer in good operating condition. 2. HP laptop repair skills and troubleshootingForeword
With the continuous advancement of technology, laptops play an increasingly important role in our lives. As a highly portable and powerful device, laptops have become a necessity for many people for daily work and entertainment. However, just like any other electronic device, HP laptops can suffer from various malfunctions and issues. This article will provide you with some HP laptop repair tips and troubleshooting methods.
Common problems and solutions
1. The computer cannot be turned on
If your HP laptop cannot be turned on, first check whether the power adapter is firmly connected and whether the battery is charging normally. If the problem persists, try pressing and holding the power button for 5 seconds, then release it and try turning on the phone again.2. Blue Screen or Black Screen
When your HP laptop has a blue screen or black screen, it may be because of an operating system crash or driver issue. You can try to restart your computer and press F8 or F11 during startup to enter safe mode, and then perform related troubleshooting.3. The battery is not charging
If your HP laptop battery cannot be charged, you can first ensure that the power adapter is connected properly. If the problem persists, you can try removing the battery from the computer, wiping the metal contacts with a clean cloth and reinserting it.4. WiFi connection problem
When your HP laptop cannot connect to WiFi, you can first make sure that the wireless network is turned on and within range. Then, try restarting the router and updating the wireless card driver. If the problem persists, you can try forgetting and reconnecting to the WiFi network.5. Keyboard failure
If your HP laptop keyboard fails, you can try cleaning the dust and debris around the keyboard. If the problem persists, you may need to replace the keyboard or contact professional service personnel.Seek professional repair help
If you encounter a more complex problem, or if none of the above methods can solve your problem, it is recommended to seek professional HP laptop repair help. HP usually provides repair centers or authorized service outlets where you can send your computer for repair.
Summary
In this article, we have introduced some common HP laptop problems and repair methods, including computer not turning on, blue screen or black screen, battery not charging, WiFi connection issues and keyboard failure. I hope this information will help you solve the problems you are encountering on your HP laptop. If your problem is too complex or impossible to solve, don't hesitate to seek professional repair help.
Thank you for reading, I hope this article has provided you with valuable information and can help you better understand HP laptop repair and troubleshooting methods.
3. Tube bending machine troubleshooting?
Check whether the encoder circuit is in poor contact. Generally, if the angle is broken, it will always display 0 degrees. It won't be good or bad. There should be some poor contact in the wiring.
4. Troubleshooting of punch press?
The following principles should be followed when diagnosing faults.
1. First external, then internal
The failure rate of modern CNC machine tools itself has become lower and lower, and most of the faults are not caused by the system itself. Maintenance personnel should check one by one from the outside to the inside, and try to avoid random unpacking and disassembly, otherwise the fault will be magnified, resulting in loss of machine tool accuracy and reduced performance.
2. Main machine first, then electrical
Generally speaking, main machine faults are easier to detect, while it is more difficult to diagnose CNC system and electrical faults. Judging from actual experience, a large part of the failures of CNC machine tools are caused by the failure of the host part. Therefore, before troubleshooting, you should first pay attention to eliminating mechanical faults, which can often achieve twice the result with half the effort.
3. Static first, then dynamic
In the static state of the lathe when the power is off, through understanding, observation, testing, and analysis, it is confirmed that after powering on, it will not cause fault expansion or accidents, and then the lathe can be powered on. In the running state, dynamic observation, inspection and testing are carried out to find faults. For those that may cause destructive failures after powering on, the danger must be eliminated before powering on.
4. Simple first, then complex
When multiple faults are intertwined, easy problems should be solved first, and then more difficult problems should be solved. Difficult problems may become easier when simple problems are solved.
5. First general, then special
When troubleshooting a certain fault, first consider the most common possible causes, and then analyze the special causes that rarely occur.
When there is an alarm or failure in the CNC system, maintenance personnel should not rush to deal with it, but should conduct more observations and experiments.
1. Fully investigate the fault site
This is an important means for maintenance personnel to obtain first-hand information. On the one hand, it is necessary to investigate the operator, ask in detail the entire process of the failure, check the fault record, understand what happened, what measures were taken, etc.; on the other hand, it is necessary to conduct a detailed investigation of the site. From the appearance of the system to the printed circuit boards inside the system, you should carefully check whether there are any abnormalities. Only after confirming that there is no danger when the system is powered on can the power be turned on, and observe any abnormalities in the system, the content displayed on the CRT, etc.
2. Carefully analyze the cause of the failure
The current CNC system is relatively low in intelligence, and the system cannot automatically diagnose the exact cause of the failure. Often the same alarm number can have multiple causes, and it is impossible to narrow the fault down to a specific component. Therefore, when analyzing the cause of the failure, you must have a broad mind. It often happens that a certain part of the system is faulty due to self-diagnosis, but the origin is not in the CNC system, but in the mechanical part. Therefore, whether it is a CNC system, machine tool power supply, or mechanical, hydraulic, pneumatic circuit, etc., as long as there are possible causes of the failure, they must be listed as comprehensively as possible, comprehensive judgment and screening should be carried out, and then through necessary tests, Achieve the purpose of diagnosis and final troubleshooting
5. Substance GPU troubleshooting
Blog article: Substance GPU troubleshooting
With the continuous development of technology, GPU (graphics processor) plays an increasingly important role in our daily lives. The more important the role. Whether it is games, video editing or artificial intelligence applications, the powerful computing power of GPU is required. However, sometimes we may encounter issues with GPU failure, at which point troubleshooting is required. This article will cover some common GPU troubleshooting methods.
1. Common faults and causes
1. Slow operation: This may be due to incompatible, outdated or damaged drivers, or problems with the GPU hardware itself.
2. Troubleshooting steps
Check the driver: Make sure the driver is compatible and the latest version. If the driver is corrupted or incompatible, it may cause your GPU to run slowly or cause other problems. Check the hardware: Check the GPU hardware for damage or dust buildup, which may cause cooling issues and thus affect the performance of the GPU. Use GPU tools: Use specialized GPU tools (such as GPU-Z) to monitor the running status of the GPU and check if there are any abnormalities.3. Other precautions
When troubleshooting, please make sure to comply with relevant safety regulations to avoid damage to the hardware. In addition, if you cannot solve the problem yourself, it is recommended to seek professional help.
Summary
This article introduces the relevant knowledge of Substance GPU troubleshooting, including common faults and causes, troubleshooting steps, and some precautions. By following these steps, we can effectively solve the GPU failure problem and ensure the normal operation of the computer.
6. What kind of work is done in network troubleshooting?
We often encounter various wireless network failures. Many users cannot cope with it, thus affecting the efficiency of Internet access. Xiaolin Computer has made the following analysis on these wireless network troubleshooting:
Step 1: Check the network configuration
The network troubleshooting process can be achieved by verifying the host you know . The method is to run the IPCONFIG command on both hosts to ensure that the IP addresses they use are within the expected range. Although the operation is very basic, running the IPCONFIG command will expose the source of the problem. For example, a system that is not receiving an IP address may be because the DHCP range has been exhausted.
Running the IPCONFIG command alone displays the IP address, subnet mask, and default gateway assigned to each network adapter. If there are no problems with these values, you can go a step further and run the IPCONFIG /ALL command. This will display the DNS server assignments for each network adapter. It is important to verify that the system is using the expected DNS servers.
Step 2: Test Name Resolution
After verifying the IP address configuration of the source and destination hosts, you can verify that name resolution is working properly. There are various tools for testing DNS name resolution, but the easiest way is to enter NSLOOKUP command and enter the fully qualified domain name of the other host.
The NSLOOKUP command can display the DNS server in use and tell you whether the DNS server is authoritative for the specified host.
After receiving the results from NSLOOKUP, please check to make sure the results are as expected. The IP address of the DNS server should match the IP address of the DNS server that the host's network adapter is configured to use. Likewise, the name resolved address should match the IP address that has been assigned to the remote host (or a service running on the remote host).
Step 3: Verify Network Path
If your check is fine so far and has produced the expected results, then the process is The next step is to verify the network path to the remote host. The easiest way is to enter the Tracert command followed by the fully qualified domain name of the remote host. The tracert command will display the route that the packet took when routed to the remote host.
If some hops are reported as "Request Timeout", don't worry too much as it just means the host is configured not to respond to ICMP messages. It is important to ensure that Tracert does not show that the destination is unreachable (sometimes indicated by the !H indicator). The destination host unreachable message indicates that there is no route to the destination or the IP address cannot be resolved to an L2 address.
Step 4: Test the responsiveness of the remote host
The next step in the troubleshooting process is to test whether you can communicate with the remote host. One time it might just mean pinging the remote host. Unfortunately, hosts are often configured not to respond to ping requests, so this test may not be feasible.
In this case some kind of test needs to be done to see if you can get the host to respond. After all, the response verifies that there is a connection between the two hosts and that the remote host is still online.
The types of responsiveness tests that can be used vary greatly depending on the configuration of the remote host. If you cannot use the ping command, you can also verify the responsiveness of the remote host by establishing a remote PowerShell session
Step 5: Test the remote service
If you have confirmed that the local and remote hosts are configured correctly, and that name resolution and basic connections are working properly in both directions, the problem most likely exists higher up in the network stack. For example, if the target host is a web server, even if the basic communication test is successful, the system service is stopped or there is a permission issue. This is when you need to test any services provided by the remote host.
It is important to note that sometimes services may be adversely affected by lower-level dependencies. For example, I once encountered some serious communication problems on Exchange Server. After exhaustive troubleshooting work, I finally traced the problem to the wrong time setting of the system.
Network Troubleshooting: More Than Just Science
Sadly, there is no more effective solution to network troubleshooting (although there are some great third-party diagnostic tools available). Any time you encounter a network problem, ignore as much of the complexity of the network as possible and focus on checking the basics. Even if these steps don't reveal the cause of the problem, they can help you narrow down the problem. Learn more about it
7. Troubleshooting: A practical guide to solving laptop power problems
Common laptop power problems and solutions
Computer laptop power problems are one of the troubles users often encounter in daily use. Problems such as the inability to turn on the phone, the inability to charge the battery, and the flashing power indicator light may affect the user experience. When encountering these problems, users can troubleshoot and solve the problem according to the following content.
Cannot turn on
If the laptop cannot turn on, you should first check whether the power adapter is connected properly and make sure the socket is powered. If the adapter is connected normally, you can try to unplug the power adapter, take out the battery, press and hold the power button for about 30 seconds, then reinsert the battery and adapter and try to turn on the phone again.
The battery cannot be charged
When the laptop cannot be charged after connecting the power adapter, first check whether the adapter and power cord are damaged, and confirm whether the power socket is normal. In addition, you can also check whether the battery driver is normal in the device manager, or make relevant settings in the BIOS.
Power light flashing
Some laptops may not turn on when the power light flashes, this may be due to hardware failure or device overheating protection. Users can consult the relevant manuals according to the computer model, troubleshoot according to the methods in the manual, or seek after-sales service support.
Maintenance and care
In order to avoid power problems, users should also pay attention to the care and maintenance of their laptops during daily use. Regularly cleaning the cooling holes, maintaining battery health, and avoiding excessive discharge are all important methods to maintain the computer power system.
In short, for laptop power problems, users can troubleshoot through the above methods and seek professional technical support when necessary. With correct methods and maintenance, the stability and durability of your computer can be effectively improved.
Thank you for reading this guide, I hope these contents can help you better solve laptop power problems and improve your use experience.
8. How to troubleshoot common faults of the relief valve?
When the relief valve is in use, common faults include noise, vibration, radial clamping of the valve core, and pressure regulation failure.
(1) Noise and Vibration
The components that are prone to noise in hydraulic devices are generally considered to be pumps and valves. Among the valves, relief valves and electromagnetic reversing valves are the main ones. There are many factors that produce noise. There are two types of noise from the relief valve: flow velocity sound and mechanical sound. The flow velocity sound is mainly caused by oil vibration, cavitation and hydraulic impact. Mechanical sound is mainly caused by the impact and friction of parts in the valve.
(1) Noise caused by uneven pressure
The pilot valve part of the pilot-operated relief valve is a vibration-prone part. When overflow occurs under high pressure, the axial opening of the pilot valve is very small, only 0.003 to 0.006 cm. The flow area is very small and the flow velocity is very high, up to 200 meters/second, which can easily cause uneven pressure distribution, causing the radial force of the poppet valve to be unbalanced and causing vibration. In addition, the ovality produced during the processing of the poppet valve and poppet valve seat, dirt sticking to the pilot valve port, and deformation of the pressure regulating spring can also cause vibration of the poppet valve. Therefore, it is generally believed that the pilot valve is the source of noise.
Due to the existence of elastic elements (springs) and moving masses (poppet valves), a condition for oscillation is formed, and the front cavity of the pilot valve also acts as a resonance cavity, so the vibration of the poppet valve can easily cause the entire The resonance of the valve causes noise. When noise occurs, it is usually accompanied by violent pressure jumps.
(2) Noise generated by cavitation
When air is sucked into the oil due to various reasons, or when the oil pressure is lower than the atmospheric pressure, part of the air dissolved in the oil will precipitate to form bubbles. These The bubbles have a larger volume in the low-pressure area. When the oil flows to the high-pressure area, they are compressed and the volume suddenly becomes smaller or the bubbles disappear. On the contrary, if the volume is originally small in the high-pressure area, but when it flows to the low-pressure area, A sudden increase in volume, a phenomenon in which the volume of bubbles in oil changes rapidly. The sudden change in bubble volume will produce noise, and because this process occurs in an instant, it will cause local hydraulic shock and vibration. The pilot valve port and main valve port of the pilot relief valve have large changes in oil flow rate and pressure, and cavitation is prone to occur, resulting in noise and vibration.
(3) Noise generated by hydraulic shock
When the pilot relief valve is unloading, pressure shock noise will occur due to a sudden drop in pressure in the hydraulic circuit. The more high-pressure and large-capacity working conditions the greater the impact noise. This is caused by the hydraulic impact caused by the short unloading time of the relief valve. During unloading, the oil flow rate changes sharply, causing a sudden change in pressure, causing The impact of pressure waves. The pressure wave is a small shock wave, which itself produces very little noise. However, when the oil is transmitted to the system, if it resonates with any mechanical part, it may increase vibration and noise. Therefore, when hydraulic impact noise occurs, it is usually accompanied by system vibration.
(4) Mechanical noise
The mechanical noise emitted by the pilot relief valve generally comes from the impact of parts and the friction of parts due to machining errors.
파일럿 릴리프 밸브에서 나오는 소음 중에는 기계적 고주파 진동음이 있는 경우가 있는데, 이를 일반적으로 자려진동음이라고 합니다. 메인 밸브와 파일럿 밸브의 고주파 진동으로 인해 발생하는 소리입니다. 발생률은 오일 회수 파이프라인의 구성, 유속, 압력, 오일 온도(점도) 등과 같은 요인과 관련이 있습니다. 일반적으로 파이프라인 직경이 작고 유량이 작고 압력이 높으며 오일 점도가 낮을 때 자려 진동의 발생률이 높습니다.
파일럿 릴리프 밸브의 소음 및 진동을 줄이거나 없애기 위한 조치는 일반적으로 파일럿 밸브 부분에 진동 감쇠 부품을 추가하는 것입니다.
진동 흡수 슬리브는 일반적으로 파일럿 밸브의 전면 공동, 즉 공진 공동에 고정되어 자유롭게 움직일 수 없습니다. 댐핑 슬리브에는 다양한 댐핑 구멍이 제공되어 댐핑을 높이고 진동을 제거합니다. 또한, 공진공동에 부품을 추가함으로써 공진공동의 부피가 감소하고, 부압 하에서 오일의 강성이 증가하게 되는데, 강성이 높은 부품은 공진이 잘 일어나지 않는다는 원리에 따른 것이다. 공명 가능성이 줄어들 수 있습니다.
진동 흡수 패드는 일반적으로 공진 공동과 협력하여 자유롭게 움직일 수 있습니다. 진동 흡수 패드의 앞면과 뒷면에 조절 홈이 있어 오일이 흐를 때 원래의 흐름 상황을 변경하는 댐핑 효과를 생성할 수 있습니다. 진동 흡수 패드의 추가로 인해 진동 요소가 추가되어 원래의 공진 주파수를 방해합니다. 공진 캐비티에 진동 흡수 패드가 추가되어 압력을 받을 때 오일의 부피가 줄어들고 강성이 증가하여 공진 가능성이 줄어듭니다.
진동 흡수 나사 플러그에는 공기 저장 구멍과 스로틀링 모서리가 있습니다. 공기 저장 구멍에 공기가 있기 때문에 압축된 공기는 진동을 흡수하는 효과가 있습니다. 미세 진동 흡수 장치와 동일합니다. 작은 구멍 안의 공기가 압축되면 오일이 채워지고, 팽창하면 오일이 강제로 빠져나가게 되어 추가적인 흐름이 추가되어 원래의 흐름 상황이 바뀌게 됩니다. 따라서 소음과 진동도 줄이거나 없앨 수 있습니다.
또한 릴리프 밸브 자체를 잘못 조립하거나 사용하는 경우에도 진동과 소음이 발생합니다. 예를 들어, 3섹션 동심 릴리프 밸브는 조립 중 3개 동심 섹션의 조정이 부적절하고, 사용 중 유량이 너무 크거나 작으며, 포핏 밸브가 비정상적으로 마모되는 등의 문제가 있습니다. 이런 경우에는 조정 상태를 주의 깊게 확인하거나 부품을 교체해야 합니다.
릴리프 밸브의 일반적인 고장 해결 방법
(2) 밸브 코어의 방사형 클램핑
가공 정밀도의 영향으로 메인 밸브 코어가 방사형으로 클램핑되어 메인 밸브가 열리고 압력이 가해지지 않거나 메인 밸브가 닫히지 않고 오염으로 인해 방사형 클램핑이 발생합니다.
(3) 압력 조절 실패
사용 중 릴리프 밸브에서 압력 조절 실패가 발생할 수 있습니다. 파일럿 릴리프 밸브가 압력을 조절하지 못하는 경우에는 두 가지 상황이 있습니다. 하나는 압력 조절 핸드휠이 압력을 형성할 수 없거나 압력이 정격 값에 도달할 수 없는 경우이고, 다른 하나는 조절 핸드휠의 압력이 감소하지 않는 경우입니다. 또는 계속해서 증가하고 있습니다. 압력 조절 실패가 발생하면 여러 가지 이유로 밸브 코어의 반경 방향 클램핑 외에도 다음과 같은 이유가 있습니다.
첫 번째는 메인 밸브 본체(2)의 댐퍼가 막혀 오일이 압력이 메인 밸브의 상부 챔버와 가이드로 전달되지 않습니다. 밸브의 전면 공동에서 파일럿 밸브는 메인 밸브의 압력을 조절하는 능력을 상실합니다. 메인 밸브의 상부 챔버에는 오일 압력이 없고 스프링 힘이 매우 작기 때문에 오일 입구 챔버의 압력이 매우 낮을 때 메인 밸브는 스프링 힘이 매우 작은 직동식 릴리프 밸브가 됩니다. , 메인 밸브가 릴리프 밸브를 열면 시스템이 압력을 형성할 수 없습니다.
압력이 정격값에 도달할 수 없는 이유는 압력 조절 스프링이 변형되었거나 잘못 선택되었거나, 압력 조절 스프링의 압축 행정이 불충분하거나, 밸브의 내부 누출이 너무 크거나, 포핏 밸브의 포핏 밸브 때문입니다. 파일럿 밸브 부분이 과도하게 마모되었습니다.
두 번째는 댐퍼(3)가 막혀 오일 압력이 포핏 밸브로 전달되지 못하여 파일럿 밸브가 메인 밸브의 압력을 조절하는 능력을 상실한 것입니다. 댐퍼(작은 구멍)가 막힌 후에는 어떤 압력에서도 포핏 밸브가 열려 오일이 넘치지 않습니다. 밸브에는 항상 메인 밸브의 상부 챔버와 하부 챔버의 압력이 동일하기 때문입니다. 메인 밸브 코어 상단의 환형 압력 베어링 영역은 하단에 환형 압력 베어링 영역이 있으므로 메인 밸브는 항상 닫혀 있고 부하가 증가함에 따라 메인 밸브 압력이 증가하지 않습니다. . 액추에이터가 작동을 멈추면 시스템 압력이 무한정 증가합니다. 이러한 이유 외에도 외부 제어 포트가 막혀 있는지, 포핏 밸브가 제대로 설치되어 있는지 등을 확인하는 것도 필요합니다.
(4) 기타 불량
릴리프 밸브 조립 또는 사용 중 오링 씰, 결합 씰 링의 손상 또는 장착 나사 및 파이프 조인트의 풀림으로 인해 과도한 누출이 발생할 수 있습니다.
포핏 밸브나 메인 밸브 코어가 너무 마모되거나 씰링 표면의 접촉이 불량한 경우 과도한 내부 누출이 발생하고 심지어 정상적인 작동에 영향을 미칠 수 있습니다.
전자기 릴리프 밸브의 일반적인 결함으로는 파일럿 솔레노이드 밸브 고장, 메인 밸브의 압력 조절 실패 및 하역 중 충격 소음 등이 있습니다. 후자는 추가된 버퍼를 조정하여 줄이거나 제거할 수 있습니다. 버퍼가 없으면 메인 밸브 오버플로 포트에 배압 밸브를 추가할 수 있습니다. (압력은 일반적으로 5kgf/cm2 정도, 즉 0.5MPa 정도로 조정됩니다.)
9. 버스 결함을 해결하는 방법은 무엇입니까?
정전이 발생하면 먼저 메인 스위치를 분리한 후 각 라인의 부하를 분리하고 하나씩 확인하세요
10. Tianlong ECU의 문제 해결?
문제 해결 방법은 다음과 같습니다
1. Tianlong에 EECU 오류가 발생한 경우 CAN 라인에 문제가 있거나 CAN 라인의 플러그가 느슨하거나 접촉 불량일 수 있습니다.
2. 조사 결과 셧다운 스위치 하니스 커넥터에 물이 들어가 접촉 핀이 부식된 것으로 확인되었습니다.
3. 접점 핀의 녹 및 방청처리를 제거한 후 결함을 다시 연결하여 문제를 해결합니다.
The above is the detailed content of Freezer Troubleshooting. For more information, please follow other related articles on the PHP Chinese website!

Hot AI Tools

Undresser.AI Undress
AI-powered app for creating realistic nude photos

AI Clothes Remover
Online AI tool for removing clothes from photos.

Undress AI Tool
Undress images for free

Clothoff.io
AI clothes remover

Video Face Swap
Swap faces in any video effortlessly with our completely free AI face swap tool!

Hot Article

Hot Tools

Notepad++7.3.1
Easy-to-use and free code editor

SublimeText3 Chinese version
Chinese version, very easy to use

Zend Studio 13.0.1
Powerful PHP integrated development environment

Dreamweaver CS6
Visual web development tools

SublimeText3 Mac version
God-level code editing software (SublimeText3)

Hot Topics










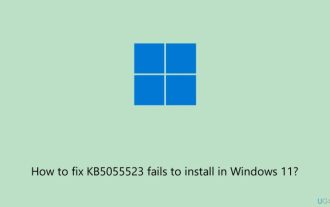
KB5055523 update is a cumulative update for Windows 11 version 24H2, released by Microsoft on April 8, 2025, as part of the monthly Patch Tuesday cycle, to offe
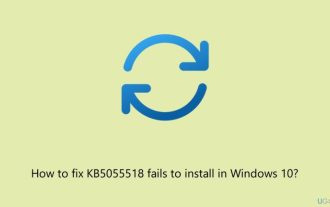
Windows update failures are not uncommon, and most users have to struggle with them, most often becoming frustrated when systems fail to install critical patche
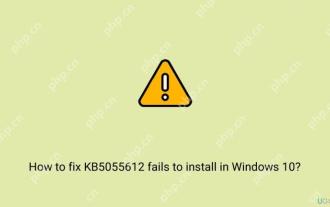
Windows updates are a critical part of keeping the operating system stable, secure, and compatible with new software or hardware. They are issued on a regular b
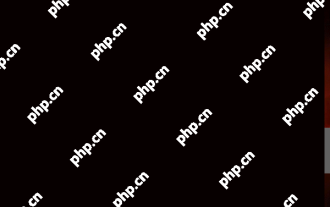
Troubleshooting The Elder Scrolls IV: Oblivion Remastered Launch and Performance Issues Experiencing crashes, black screens, or loading problems with The Elder Scrolls IV: Oblivion Remastered? This guide provides solutions to common technical issues.
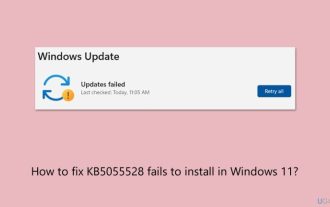
Windows updates are essential to keep your system up to date, secure, and efficient, adding security patches, bug fixes, and new functionality for Windows 11 us
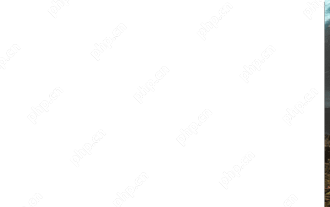
Solve the problem of failure of the PC version of "Clair Obscur: Expedition 33" Have you also encountered the problem that the PC version of the "Clair Obscur: Expedition 33" controller does not work properly? Don't worry, you are not alone! This article will provide you with a variety of effective solutions. "Clair Obscur: Expedition 33" has been launched on PlayStation 5, Windows and Xbox Series X/S platforms. This game is an engaging turn-based RPG that emphasizes precise timing. Its uniqueness is the perfect blend of strategic and rapid response. Smooth operation
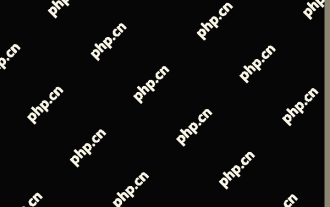
Solve the UE-Sandfall game crash problem in "Clair Obscur: Expedition 33" "Clair Obscur: Expedition 33" has been widely expected by players after its release, but many players encountered the error of UE-Sandfall crashing and closing when starting the game. This article provides three solutions to help you smooth the game. Method 1: Change the startup options Change the Steam startup options to adjust game performance and graphics settings. Try setting the startup option to "-dx11". Step 1: Open the Steam library, find the game, and right-click to select "Properties". Step 2: Under the General tab, find the Startup Options section.
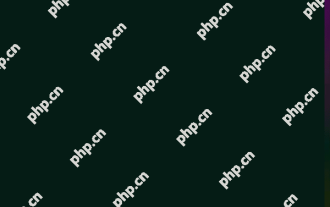
Windows 11 KB5055528 (released on April 8, 2025) Update detailed explanation and troubleshooting For Windows 11 23H2 users, Microsoft released the KB5055528 update on April 8, 2025. This article describes the improvements to this update and provides a solution to the installation failure. KB5055528 update content: This update brings many improvements and new features to Windows 11 23H2 users: File Explorer: Improved text scaling and improved accessibility to the file opening/save dialog and copy dialog. Settings page: Added "Top Card" function to quickly view processor, memory, storage and G
