What is the definition of industrial robot?
Industrial robots refer to multi-joint manipulators or multi-degree-of-freedom machine devices that are widely used in the industrial field. They have a certain degree of automation and can rely on their own power energy and control capabilities to achieve various industrial processing and manufacturing functions.
The operating environment of this tutorial: Windows 7 system, Dell G3 computer.
Definition of industrial robots (robots for the industrial field)
Industrial robots are multi-joint manipulators or multi-freedom robots that are widely used in the industrial field. A high degree of machine device with a certain degree of automation, which can rely on its own power energy and control capabilities to achieve various industrial processing and manufacturing functions.
Industrial robots are widely used in various industrial fields such as electronics, logistics, and chemicals.
Composition of industrial robots
Generally speaking, industrial robots are composed of three parts and six subsystems.
The three major parts are the mechanical part, the sensing part and the control part.
The six subsystems can be divided into mechanical structure system, drive system, perception system, robot-environment interaction system, human-computer interaction system and control system.
1. Mechanical structure system
From the perspective of mechanical structure, industrial robots are generally divided into series robots and parallel robots. The characteristic of the tandem robot is that the movement of one axis will change the coordinate origin of the other axis, while the movement of one axis of the parallel robot will not change the coordinate origin of the other axis. Early industrial robots all used series mechanisms. A parallel mechanism is defined as a closed-loop mechanism in which the moving platform and the fixed platform are connected through at least two independent kinematic chains. The mechanism has two or more degrees of freedom and is driven in parallel. The parallel mechanism has two components, the wrist and the arm. The arm activity area has a great impact on the activity space, and the wrist is the connection part between the tool and the main body. Compared with series robots, parallel robots have the advantages of large rigidity, stable structure, large load-bearing capacity, high micro-motion accuracy, and small motion load. In terms of position solution, the forward solution of the series robot is easy, but the inverse solution is very difficult; on the contrary, the forward solution of the parallel robot is difficult, but the inverse solution is very easy.
2. Drive system
The drive system is a device that provides power to the mechanical structure system. According to different power sources, the transmission modes of the drive system are divided into four types: hydraulic, pneumatic, electrical and mechanical. Early industrial robots were hydraulically driven. Because the hydraulic system has problems such as leakage, noise, and low-speed instability, and the power unit is bulky and expensive, currently only large heavy-duty robots, parallel processing robots, and some special applications use hydraulic-driven industrial robots. Pneumatic drive has the advantages of fast speed, simple system structure, convenient maintenance and low price. However, the working pressure of the pneumatic device is low and it is difficult to position accurately. It is generally only used to drive the end effector of industrial robots. Pneumatic hand grippers, rotating cylinders and pneumatic suction cups can be used as end effectors for grabbing and assembling workpieces with medium and small loads. Electric drive is the most commonly used driving method at present. It is characterized by easy access to power, fast response, large driving force, convenient signal detection, transmission and processing, and can adopt a variety of flexible control methods. The drive motor generally adopts stepper control. Currently, direct drive motors are also used for electric motors or servo motors, but the cost is higher and the control is more complicated. The reducer that matches the motor generally uses a harmonic reducer, a cycloidal pinwheel reducer or a planetary gear reducer. Due to the large number of linear drive requirements in parallel robots, linear motors have been widely used in the field of parallel robots.
3. Perception system
The robot perception system converts various internal state information and environmental information of the robot from signals into signals that can be understood and applied by the robot itself or between robots. Data and information, in addition to the need to perceive mechanical quantities related to its own working status, such as displacement, speed and force, visual perception technology is an important aspect of industrial robot perception. The visual servo system uses visual information as a feedback signal to control and adjust the position and attitude of the robot. Machine vision systems are also widely used in various aspects of quality inspection, workpiece identification, food sorting, and packaging. The perception system consists of internal sensor modules and external sensor modules. The use of smart sensors improves the robot's mobility, adaptability and intelligence.
4. Robot-environment interaction system
The robot-environment interaction system is a system that realizes the interconnection and coordination between robots and equipment in the external environment. The robot and external equipment are integrated into a functional unit, such as processing and manufacturing unit, welding unit, assembly unit, etc. Of course, multiple robots can also be integrated into a functional unit to perform complex tasks.
5. Human-computer interaction system
The human-computer interaction system is a device for people to communicate with robots and participate in robot control. For example: computer standard terminal, command console, information display panel, danger signal alarm, etc.
6. Control system
The task of the control system is to control the robot's actuator to complete specified movements and functions based on the robot's operating instructions and the signals fed back from the sensors. If the robot does not have information feedback characteristics, it is an open-loop control system; if it has information feedback characteristics, it is a closed-loop control system. According to the control principle, it can be divided into program control system, adaptive control system and artificial intelligence control system. According to the form of control motion, it can be divided into point control and continuous trajectory control.
For more related knowledge, please visit the FAQ column!
The above is the detailed content of What is the definition of industrial robot?. For more information, please follow other related articles on the PHP Chinese website!

Hot AI Tools

Undresser.AI Undress
AI-powered app for creating realistic nude photos

AI Clothes Remover
Online AI tool for removing clothes from photos.

Undress AI Tool
Undress images for free

Clothoff.io
AI clothes remover

AI Hentai Generator
Generate AI Hentai for free.

Hot Article

Hot Tools

Notepad++7.3.1
Easy-to-use and free code editor

SublimeText3 Chinese version
Chinese version, very easy to use

Zend Studio 13.0.1
Powerful PHP integrated development environment

Dreamweaver CS6
Visual web development tools

SublimeText3 Mac version
God-level code editing software (SublimeText3)

Hot Topics
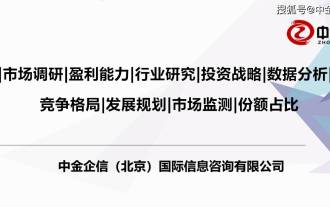
2024 Industrial Robot Industry Application Field Market Analysis and Industry Development Trend Forecast Report Publisher: CICC Enterprise Trust International Consulting "2024-2030 Industrial Robot Industry Market Research and Strategic Planning Investment Forecast Report" CICC Enterprise Trust International Consulting related report recommendations (2023-2024 ) "Industrial Robot Project Proposal - Prepared by CICC Enterprises" "Individual Champion Market Share - Industrial Robot Market Share Certification Report (2024 Edition)" "Released by CICC Enterprises - "In-depth Investigation into the Market Development of the Industrial Robot Industry and Investment Strategy Feasibility Report (2023 Edition)》《2023-2029 China's Industrial Robot Special Lubricants/Grease Market Development Analysis and Future Investment Potential Feasibility Report》《2023-202
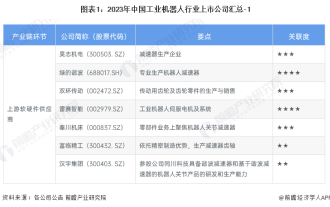
——Rewrite the title: Comprehensive comparison of listed companies in the industrial robot industry in 2023: Comprehensive comparison of major listed companies in the industry in terms of business layout, performance and business planning: Robot (300024); New Star (002527); Eston (002747) ; Inovance Technology (300124); Evert (688165), etc. The core data of this article: summary of listed companies; business layout of listed companies; performance of listed companies; business planning of listed companies 1. Summarizes the situation of listed companies in the industrial robot industry Industrial Robots The core components of the industry, such as robot control systems, reducers and servo systems, play an important role in the cost structure of industrial robots. Midstream robot manufacturing companies typically engage in vertical integration to
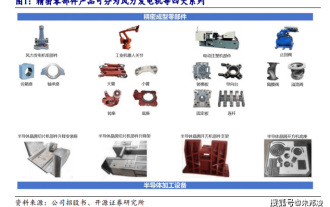
Kunbo Seiko will be launched on the 23rd. The company has two underexplored highlights, one is industrial robot arms, and the other is semiconductor concept. Kunbo Precision produces industrial robot arms and other industrial automation equipment parts. Kunbo Precision high-end equipment precision molding parts products are based on applications. The fields can be divided into four series: wind turbines, industrial automation equipment, offshore engineering equipment, and semiconductor processing equipment. Wind turbine parts include wind power gear box seats, spindle bearing seats, etc.; industrial automation equipment parts include electric precision injection molding machine templates, oil cylinders, industrial robot arms, swivel seats and other main joint parts; offshore engineering equipment parts include seawater Desalination valves, offshore oil coating and cutting device components; semiconductor processing equipment components including grinding and polishing discs, cutting fuselage components
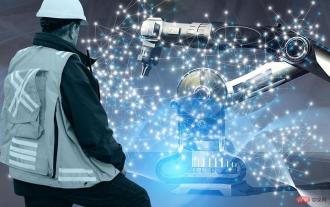
Today, industrial robots are used in almost all industries. They bring many benefits to manufacturing facilities and pave the way for the smart factories of the future. However, there are some limitations that manufacturers should consider when selecting robotic equipment. Demand for automated processes is increasing, with the industrial robot market expected to reach $31.3 billion by 2028, Fortune Business Insights reports. Manufacturers are increasingly aware of the potential business and production benefits of implementing robots. However, industrial robots are not without their drawbacks. Here are some of the most common limitations, along with some suggestions from manufacturers on how to overcome them. Affordability Generally speaking, industrial robots require a significant upfront investment, including additional installation and configuration costs. Manufacturers also need to consider future maintenance costs and
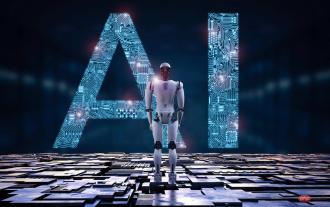
How do industrial welding robots help users improve welding efficiency? Industrial welding robots are automated mechanical equipment used for welding operations. Traditional welding has problems such as difficult welding processes, low efficiency, difficulty in recruiting workers, and unstable welding quality. Industrial welding robot applications help users solve problems and use industrial welding robots to put into production. This article takes you through the advantages of industrial welding robots. 1. Intelligent welding control system Industrial welding robots have multiple sensors. The arc sensor can automatically find the position. The arc sensor uploads the welding information to the control system. The control system can release just the right welding material for filler welding according to the programming parameters. seams, reducing the repair rate of welded parts and improving welding efficiency. 2. Multi-axis cooperation improves welding flexibility and industrial welding
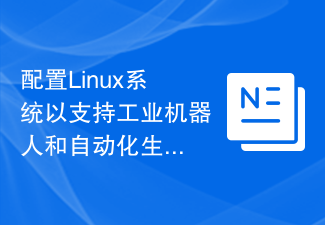
Configuring Linux systems to support industrial robots and automated production development With the rapid development of industrial robots and automated production, more and more companies are beginning to use Linux systems to support their production development. Linux system has good stability, flexibility and customizability, which makes it an ideal choice. This article will describe how to configure a Linux system to support industrial robots and automated production development, and provide some code examples. To install a Linux system, first, you need to choose a suitable Linux
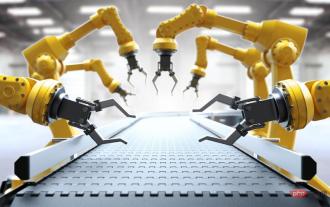
A robot is a machine that has more degrees of freedom in three-dimensional space and can realize many anthropomorphic actions and functions, while industrial robots are robots used in industrial production. Its characteristics are: programmability, anthropomorphism, versatility, and mechatronics. What systems does an industrial robot consist of? 1. The main body of the machine is the machine base and the actuator, including the big arm, forearm, wrist and hand, which constitute a multi-degree-of-freedom mechanical system. Some robots also have walking mechanisms. Industrial robots have 6 degrees of freedom or even more. The wrist generally has 1 to 3 degrees of freedom of movement. 2. The drive system is a transmission device that enables the robot to run. According to the power source, it is divided into three categories: hydraulic, pneumatic and electric. These three types can also be combined into a composite drive system based on requirements. or via timing belt

External factors have had a huge impact on the industrial robotics industry in recent years, from the COVID-19 pandemic to geopolitical tensions and supply chain disruptions. At the same time, internal factors such as advances in technology and usability also have an impact on the development and adoption of industrial robots. Whether you are new to industrial automation or a veteran with decades of experience, there is a huge amount of information to sift through, making identifying the most impactful industry trends a real challenge. So, as 2022 comes to an end, what trends do those in the industrial robotics industry need to pay attention to? 1. Workforce and Demographics Scott Marsic, robotics product manager at Epson America, said labor shortages are the most important trend driving the adoption of industrial automation. Warehouse automation services