


What systems does an industrial robot consist of? What is the role of each?
A robot is a machine that has more degrees of freedom in three-dimensional space and can realize many anthropomorphic actions and functions, while industrial robots are robots used in industrial production. Its characteristics are: programmability, anthropomorphism, versatility, and mechatronics.
#What are the system components of industrial robots?
1. Main body
The main body is the machine base and actuator, including the big arm, forearm, wrist and hand, which constitute a multi-degree-of-freedom mechanical system. Some robots also have walking mechanisms. Industrial robots have 6 degrees of freedom or even more. The wrist generally has 1 to 3 degrees of freedom of movement.
2. Drive system
The transmission device that makes the robot run. According to the power source, it is divided into three categories: hydraulic, pneumatic and electric. These three types can also be combined into a composite drive system based on requirements. Or indirectly driven through mechanical transmission mechanisms such as synchronous belts, gear trains, and gears. The drive system has a power device and a transmission mechanism, which are used to implement the corresponding actions of the mechanism. Each of these three types of basic drive systems has its own characteristics. The current mainstream is the electric drive system.
3. Control system
controls the robot's actuator to complete specified movements and functions based on the robot's work instruction program and the signal fed back from the sensor.
Highly cost-effective microprocessors have brought new development opportunities to robot controllers, making it possible to develop low-cost, high-performance robot controllers. In order to make the system have sufficient computing and storage capabilities, robot controllers are now mostly composed of powerful ARM series, DSP series, POWERPC series, Intel series and other chips.
4. Perception system
is composed of an internal sensor module and an external sensor module to obtain information on internal and external environmental status.
Internal sensors: Sensors used to detect the status of the robot itself (such as the angle between the arms), mostly sensors that detect position and angle. Specifically: position sensor, position sensor, angle sensor, etc.
External sensors: Sensors used to detect the robot's environment (such as detecting objects, distance from objects) and conditions (such as detecting whether the grabbed object has slipped). Specifically, there are distance sensors, visual sensors, force sensors, etc.
The use of intelligent sensing systems has improved the standards of robot mobility, practicality and intelligence. The human perception system is more dexterous than robots for external world information. However, for some privileged information, sensors are more sensitive than robots. Human systems are more efficient.
5. End effector
The end effector is a component connected to the last joint of the manipulator. It is generally used to grab objects, connect with other mechanisms and perform required tasks.
The above is the detailed content of What systems does an industrial robot consist of? What is the role of each?. For more information, please follow other related articles on the PHP Chinese website!

Hot AI Tools

Undresser.AI Undress
AI-powered app for creating realistic nude photos

AI Clothes Remover
Online AI tool for removing clothes from photos.

Undress AI Tool
Undress images for free

Clothoff.io
AI clothes remover

AI Hentai Generator
Generate AI Hentai for free.

Hot Article

Hot Tools

Notepad++7.3.1
Easy-to-use and free code editor

SublimeText3 Chinese version
Chinese version, very easy to use

Zend Studio 13.0.1
Powerful PHP integrated development environment

Dreamweaver CS6
Visual web development tools

SublimeText3 Mac version
God-level code editing software (SublimeText3)

Hot Topics



The humanoid robot Ameca has been upgraded to the second generation! Recently, at the World Mobile Communications Conference MWC2024, the world's most advanced robot Ameca appeared again. Around the venue, Ameca attracted a large number of spectators. With the blessing of GPT-4, Ameca can respond to various problems in real time. "Let's have a dance." When asked if she had emotions, Ameca responded with a series of facial expressions that looked very lifelike. Just a few days ago, EngineeredArts, the British robotics company behind Ameca, just demonstrated the team’s latest development results. In the video, the robot Ameca has visual capabilities and can see and describe the entire room and specific objects. The most amazing thing is that she can also
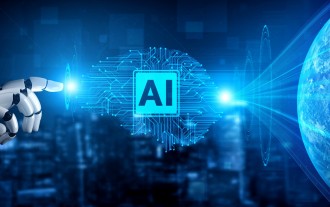
In the field of industrial automation technology, there are two recent hot spots that are difficult to ignore: artificial intelligence (AI) and Nvidia. Don’t change the meaning of the original content, fine-tune the content, rewrite the content, don’t continue: “Not only that, the two are closely related, because Nvidia is expanding beyond just its original graphics processing units (GPUs). The technology extends to the field of digital twins and is closely connected to emerging AI technologies. "Recently, NVIDIA has reached cooperation with many industrial companies, including leading industrial automation companies such as Aveva, Rockwell Automation, Siemens and Schneider Electric, as well as Teradyne Robotics and its MiR and Universal Robots companies. Recently,Nvidiahascoll
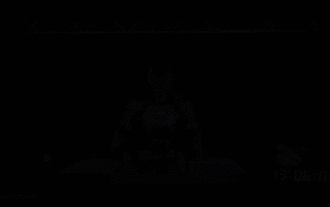
This week, FigureAI, a robotics company invested by OpenAI, Microsoft, Bezos, and Nvidia, announced that it has received nearly $700 million in financing and plans to develop a humanoid robot that can walk independently within the next year. And Tesla’s Optimus Prime has repeatedly received good news. No one doubts that this year will be the year when humanoid robots explode. SanctuaryAI, a Canadian-based robotics company, recently released a new humanoid robot, Phoenix. Officials claim that it can complete many tasks autonomously at the same speed as humans. Pheonix, the world's first robot that can autonomously complete tasks at human speeds, can gently grab, move and elegantly place each object to its left and right sides. It can autonomously identify objects
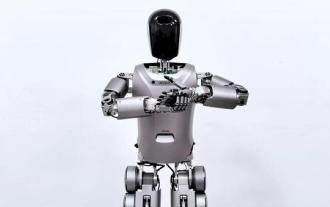
Editor of Machine Power Report: Wu Xin The domestic version of the humanoid robot + large model team completed the operation task of complex flexible materials such as folding clothes for the first time. With the unveiling of Figure01, which integrates OpenAI's multi-modal large model, the related progress of domestic peers has been attracting attention. Just yesterday, UBTECH, China's "number one humanoid robot stock", released the first demo of the humanoid robot WalkerS that is deeply integrated with Baidu Wenxin's large model, showing some interesting new features. Now, WalkerS, blessed by Baidu Wenxin’s large model capabilities, looks like this. Like Figure01, WalkerS does not move around, but stands behind a desk to complete a series of tasks. It can follow human commands and fold clothes
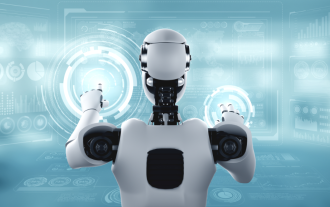
The following 10 humanoid robots are shaping our future: 1. ASIMO: Developed by Honda, ASIMO is one of the most well-known humanoid robots. Standing 4 feet tall and weighing 119 pounds, ASIMO is equipped with advanced sensors and artificial intelligence capabilities that allow it to navigate complex environments and interact with humans. ASIMO's versatility makes it suitable for a variety of tasks, from assisting people with disabilities to delivering presentations at events. 2. Pepper: Created by Softbank Robotics, Pepper aims to be a social companion for humans. With its expressive face and ability to recognize emotions, Pepper can participate in conversations, help in retail settings, and even provide educational support. Pepper's
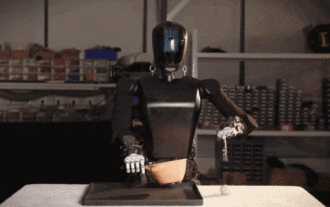
In the blink of an eye, robots have learned to do magic? It was seen that it first picked up the water spoon on the table and proved to the audience that there was nothing in it... Then it put the egg-like object in its hand, then put the water spoon back on the table and started to "cast a spell"... …Just when it picked up the water spoon again, a miracle happened. The egg that was originally put in disappeared, and the thing that jumped out turned into a basketball... Let’s look at the continuous actions again: △ This animation shows a set of actions at 2x speed, and it flows smoothly. Only by watching the video repeatedly at 0.5x speed can it be understood. Finally, I discovered the clues: if my hand speed were faster, I might be able to hide it from the enemy. Some netizens lamented that the robot’s magic skills were even higher than their own: Mag was the one who performed this magic for us.
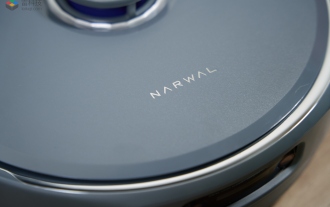
Sweeping and mopping robots are one of the most popular smart home appliances among consumers in recent years. The convenience of operation it brings, or even the need for no operation, allows lazy people to free their hands, allowing consumers to "liberate" from daily housework and spend more time on the things they like. Improved quality of life in disguised form. Riding on this craze, almost all home appliance brands on the market are making their own sweeping and mopping robots, making the entire sweeping and mopping robot market very lively. However, the rapid expansion of the market will inevitably bring about a hidden danger: many manufacturers will use the tactics of sea of machines to quickly occupy more market share, resulting in many new products without any upgrade points. It is also said that they are "matryoshka" models. Not an exaggeration. However, not all sweeping and mopping robots are
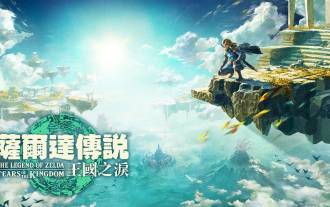
"The Legend of Zelda: Tears of the Kingdom" became the fastest-selling Nintendo game in history. Not only did Zonav Technology bring various "Zelda Creator" community content, but it also became the United States' A new engineering course at the University of Maryland (UMD). Rewrite: The Legend of Zelda: Tears of the Kingdom is one of Nintendo's fastest-selling games on record. Not only does Zonav Technology bring rich community content, it has also become part of the new engineering course at the University of Maryland. This fall, Associate Professor Ryan D. Sochol of the University of Maryland opened a course called "
