How to realize the future of warehouse technology?
Warehouse management has undergone significant changes over the past decade. The COVID-19 pandemic, greater consumer access to technology and broader demand for delivery mean profits for companies like Amazon are up $12 billion compared with pre-pandemic estimates.
But meeting the growing demand for warehouses won’t be easy. The sheer volume and velocity of orders requires digitally integrated solutions at every level. Generous help from artificial intelligence is also needed to ensure everyone’s orders arrive on time and in the expected condition.
Fortunately, the future of warehouse technology has largely kept pace with demand. Compelling new technologies like autonomous forklifts can reduce risk, increase efficiency and help warehouse managers implement the technology of the future.
Future Warehouse Technology Training
Business leaders will be able to implement the future of warehouse technology if employees are adequately trained to use, fix and improve the technology at their disposal. At first glance, this may seem simple—employees in supply chain management have been trained before—but learning to make the most of future warehouse technology may require an entirely different approach to education and training.
While previous generations of warehouse workers may have been able to learn their trade on the job, the next wave of employees may learn the tools of their trade in the classroom. That’s because the future of warehouse technology has more to do with the use of artificial intelligence (AI) and programming than it does with manual inventory management and inventory checking.
Greater access to STEM courses is needed to make skill leaps possible. Fortunately, initiatives to provide STEM courses to rural America are gaining traction. Improved internet access means rural students aged 5 to 17 can take advantage of remote learning. Increased access to STEM puts future employees in a strong position to develop and implement the future of warehouse technology.
Artificial Intelligence
Artificial intelligence has revolutionized every stage of supply chain management. Supply chain experts can now use vast amounts of raw data to predict and respond to incidents caused by pandemics, accidents and global events.
In addition, artificial intelligence technology has further improved the efficiency of warehouse operations far beyond what was imagined 20 years ago. The rise of artificial intelligence in warehouse management is a natural progression for the industry. Artificial intelligence now plays an important role in warehouse automation, helping organization, productivity, accuracy, and employee safety.
At first, switching to an automated service may seem cumbersome. But, as many warehouse clerks and distribution managers are discovering, most existing materials and equipment can be easily documented using artificial intelligence. Pallet racks, shelving, and vertical mezzanines can be processed using artificial intelligence and machine learning (ML) programs that process data at speeds that far exceed human cognitive capabilities.
Robotics
Warehouse management used to be a fairly hands-on industry, requiring workers to manually move and load goods.
Nowadays, more of the heavy lifting is being done by robotics technology following “Industry 4.0”. Today’s robotics can use new sensory data to mimic human vision and select the right package at the right time. Importantly, these robots, such as drones, can scan and enter hard-to-reach places faster than humans.
Robotics technology still requires human supervision to avoid malfunctions and prevent them from affecting all operations, so there is still a lot of progress to be made. However, as artificial intelligence develops, mistakes will become increasingly easier to predict and prevent.
Prevent Mistakes
A future dominated by artificial intelligence is both promising and daunting. While technologies like robotics and artificial intelligence will certainly improve the overall efficiency of warehouse and supply chain management, one question always looms large: What if something goes wrong?
Most concerns about artificial intelligence and new technologies are is unfounded – multinational warehouse companies don’t make decisions based on whims or incomplete data. However, warehouse management companies should not leave disruptions to chance and should take all reasonable steps to ensure that network outages do not occur.
Warehouses using automation and artificial intelligence can reduce the risk of network outages through regular internal and external analysis of all hardware and software. Internal analysis is usually easy to complete (check routers, servers, and power supplies), but external analysis (ISPs, Internet gateways, cloud services, DNs) can be a bit trickier.
Working with a reliable provider is the easiest way to ensure your external network stays online. Multi-national, cloud-based services like those offered by Google and Microsoft experience fewer outages and offer more enterprise-grade diagnostics and support that can help companies get back up and running as quickly as possible.
Conclusion
The future of warehouse technology depends largely on the development of artificial intelligence. Machine learning programs enable AI-led robots to operate with greater accuracy and efficiency. This points to a promising future in which warehouse costs decrease and the speed of picking, inventory checking and delivery increases.
The above is the detailed content of How to realize the future of warehouse technology?. For more information, please follow other related articles on the PHP Chinese website!

Hot AI Tools

Undresser.AI Undress
AI-powered app for creating realistic nude photos

AI Clothes Remover
Online AI tool for removing clothes from photos.

Undress AI Tool
Undress images for free

Clothoff.io
AI clothes remover

AI Hentai Generator
Generate AI Hentai for free.

Hot Article

Hot Tools

Notepad++7.3.1
Easy-to-use and free code editor

SublimeText3 Chinese version
Chinese version, very easy to use

Zend Studio 13.0.1
Powerful PHP integrated development environment

Dreamweaver CS6
Visual web development tools

SublimeText3 Mac version
God-level code editing software (SublimeText3)

Hot Topics


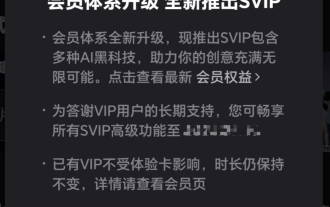
This site reported on June 27 that Jianying is a video editing software developed by FaceMeng Technology, a subsidiary of ByteDance. It relies on the Douyin platform and basically produces short video content for users of the platform. It is compatible with iOS, Android, and Windows. , MacOS and other operating systems. Jianying officially announced the upgrade of its membership system and launched a new SVIP, which includes a variety of AI black technologies, such as intelligent translation, intelligent highlighting, intelligent packaging, digital human synthesis, etc. In terms of price, the monthly fee for clipping SVIP is 79 yuan, the annual fee is 599 yuan (note on this site: equivalent to 49.9 yuan per month), the continuous monthly subscription is 59 yuan per month, and the continuous annual subscription is 499 yuan per year (equivalent to 41.6 yuan per month) . In addition, the cut official also stated that in order to improve the user experience, those who have subscribed to the original VIP
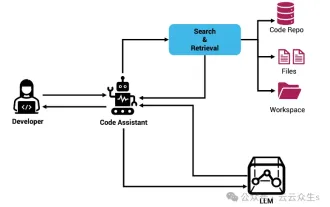
Improve developer productivity, efficiency, and accuracy by incorporating retrieval-enhanced generation and semantic memory into AI coding assistants. Translated from EnhancingAICodingAssistantswithContextUsingRAGandSEM-RAG, author JanakiramMSV. While basic AI programming assistants are naturally helpful, they often fail to provide the most relevant and correct code suggestions because they rely on a general understanding of the software language and the most common patterns of writing software. The code generated by these coding assistants is suitable for solving the problems they are responsible for solving, but often does not conform to the coding standards, conventions and styles of the individual teams. This often results in suggestions that need to be modified or refined in order for the code to be accepted into the application
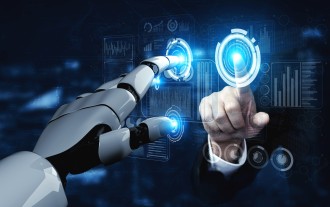
Large Language Models (LLMs) are trained on huge text databases, where they acquire large amounts of real-world knowledge. This knowledge is embedded into their parameters and can then be used when needed. The knowledge of these models is "reified" at the end of training. At the end of pre-training, the model actually stops learning. Align or fine-tune the model to learn how to leverage this knowledge and respond more naturally to user questions. But sometimes model knowledge is not enough, and although the model can access external content through RAG, it is considered beneficial to adapt the model to new domains through fine-tuning. This fine-tuning is performed using input from human annotators or other LLM creations, where the model encounters additional real-world knowledge and integrates it

To learn more about AIGC, please visit: 51CTOAI.x Community https://www.51cto.com/aigc/Translator|Jingyan Reviewer|Chonglou is different from the traditional question bank that can be seen everywhere on the Internet. These questions It requires thinking outside the box. Large Language Models (LLMs) are increasingly important in the fields of data science, generative artificial intelligence (GenAI), and artificial intelligence. These complex algorithms enhance human skills and drive efficiency and innovation in many industries, becoming the key for companies to remain competitive. LLM has a wide range of applications. It can be used in fields such as natural language processing, text generation, speech recognition and recommendation systems. By learning from large amounts of data, LLM is able to generate text
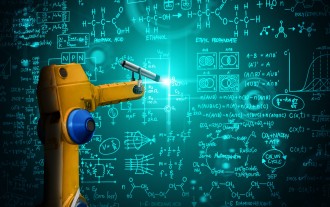
Machine learning is an important branch of artificial intelligence that gives computers the ability to learn from data and improve their capabilities without being explicitly programmed. Machine learning has a wide range of applications in various fields, from image recognition and natural language processing to recommendation systems and fraud detection, and it is changing the way we live. There are many different methods and theories in the field of machine learning, among which the five most influential methods are called the "Five Schools of Machine Learning". The five major schools are the symbolic school, the connectionist school, the evolutionary school, the Bayesian school and the analogy school. 1. Symbolism, also known as symbolism, emphasizes the use of symbols for logical reasoning and expression of knowledge. This school of thought believes that learning is a process of reverse deduction, through existing

Editor |ScienceAI Question Answering (QA) data set plays a vital role in promoting natural language processing (NLP) research. High-quality QA data sets can not only be used to fine-tune models, but also effectively evaluate the capabilities of large language models (LLM), especially the ability to understand and reason about scientific knowledge. Although there are currently many scientific QA data sets covering medicine, chemistry, biology and other fields, these data sets still have some shortcomings. First, the data form is relatively simple, most of which are multiple-choice questions. They are easy to evaluate, but limit the model's answer selection range and cannot fully test the model's ability to answer scientific questions. In contrast, open-ended Q&A
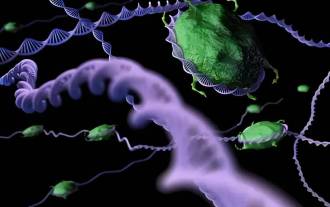
Editor | KX In the field of drug research and development, accurately and effectively predicting the binding affinity of proteins and ligands is crucial for drug screening and optimization. However, current studies do not take into account the important role of molecular surface information in protein-ligand interactions. Based on this, researchers from Xiamen University proposed a novel multi-modal feature extraction (MFE) framework, which for the first time combines information on protein surface, 3D structure and sequence, and uses a cross-attention mechanism to compare different modalities. feature alignment. Experimental results demonstrate that this method achieves state-of-the-art performance in predicting protein-ligand binding affinities. Furthermore, ablation studies demonstrate the effectiveness and necessity of protein surface information and multimodal feature alignment within this framework. Related research begins with "S
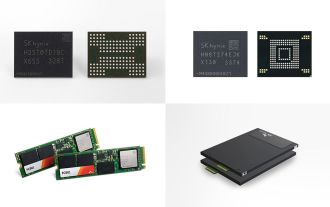
According to news from this site on August 1, SK Hynix released a blog post today (August 1), announcing that it will attend the Global Semiconductor Memory Summit FMS2024 to be held in Santa Clara, California, USA from August 6 to 8, showcasing many new technologies. generation product. Introduction to the Future Memory and Storage Summit (FutureMemoryandStorage), formerly the Flash Memory Summit (FlashMemorySummit) mainly for NAND suppliers, in the context of increasing attention to artificial intelligence technology, this year was renamed the Future Memory and Storage Summit (FutureMemoryandStorage) to invite DRAM and storage vendors and many more players. New product SK hynix launched last year
