Using AI to correct additive manufacturing errors in real time
Researchers at the Massachusetts Institute of Technology (MIT) trained a machine learning model to monitor and adjust the 3D printing process to correct errors in real time.
New materials that can be used for 3D printing are constantly being developed, but figuring out how to print with them can be a complex and costly puzzle. Typically, operators must use manual trial and error, potentially running thousands of prints, to determine the ideal parameters to print new materials consistently and efficiently.
Researchers at MIT have used artificial intelligence to streamline the process. Scientists at the agency have developed a new machine learning system that uses computer vision to observe the manufacturing process and can correct errors in how materials are handled in real time.
They used simulations to teach a neural network how to adjust printing parameters to minimize errors, and then applied the controller to a real 3D printer. The new system can print objects more accurately than other existing 3D printing controllers.
This work avoids the expensive process of printing thousands or millions of real objects to train neural networks. It could make it easier for engineers to integrate new materials into their 3D printed products, which could help them develop products with special electrical or chemical properties. It also helps technicians make adjustments to the printing process when materials or environmental conditions change unexpectedly.
"This project is really the first demonstration of building a manufacturing system that uses machine learning to learn complex control strategies," said Wojciech Matusik, professor of electrical engineering and computer science at MIT who led the project. If you have smarter manufacturing equipment that can adapt in real time to changing circumstances in the workplace to increase output or system accuracy, you can get more value out of your machines."
Pick Parameters
Determining the ideal parameters for a digital manufacturing process can be one of the most expensive parts of the process, as it requires a lot of trial and error. Once the technician finds a combination that works well, these parameters only apply to a specific situation. They have little data on whether the materials behave in other environments, on different hardware, or on new batches of materials that exhibit different properties.
Using machine learning systems is also full of challenges. First, the researchers need to measure what is happening on the 3D printer in real time.
To do this, the researchers developed a machine vision system that uses two cameras aimed at the 3D printer’s nozzle. The system shines light onto the material as it is being deposited and calculates the thickness of the material based on the amount of light that passes through. "You can think of the visual system as a pair of eyes observing this process in real time," Foshey said.
The controller will then process the images it receives from the vision system and adjust the feed rate and orientation of the printer based on any errors it sees.
But training a neural network-based controller to understand this manufacturing process is data-intensive and requires millions of prints. So the researchers built a simulator.
Successful Simulation
To better train the controller, they used a process called reinforcement learning, in which The model learns through trial and error and is rewarded. The task of the model is to select printing parameters in order to create specific objects in the simulation environment. After showing the expected output, the model is rewarded when it selects parameters that minimize the error between its print and the expected result.
In this case, "error" means that the model either allocated too much material, placing it in areas that should remain open, or did not allocate enough material, leaving The open spots below should be filled. As the model performs more simulated prints, it updates its control strategy to maximize rewards, becoming increasingly accurate.
However, the real world is messier than the simulation. In practice, conditions often vary due to small changes or noise in the printing process. So the researchers created a numerical model that approximates the noise from a 3D printer. They used this model to add noise to their simulations, producing more realistic results.
"We found it interesting that by implementing this noise model we were able to convert controls trained purely in simulation The strategy is transferred to the hardware without any physical experiments for training," Foshey said, "and afterwards, we don't need to do any fine-tuning on the actual device."
When testing the controller It prints objects more accurately than any other control method previously evaluated. It performs particularly well in infill printing, which is printing the inside of an object. Some other controllers deposited so much material that the printed objects were raised, but the researchers' controller adjusted the printing path so that the objects remained level.
Their control strategy can even understand how the material spreads after deposition and adjust parameters accordingly.
auto-adjust
"We are also able to design control strategies that can dynamically control different types of materials. So if you have a manufacturing process on site and you want to change materials, you don't have to re-validate the manufacturing process. You can just load the new material, The controller will automatically adjust," Foshey said.
Now that they have demonstrated the effectiveness of this technique for 3D printing, the researchers hope to develop controllers for other manufacturing processes. They also want to see how the method can be modified to handle multiple layers of materials or printing multiple materials at the same time. Additionally, their method assumes each material has a fixed viscosity, but future iterations could use AI to identify and adjust viscosity in real time.
MIT has a long history in additive manufacturing and has spawned several major 3D printing companies, such as Desktop Metal and VulcanForms. This work was supported in part by the FWF Lise-Meitner Program, a European Research Council Starting Grant, and the National Science Foundation.
The above is the detailed content of Using AI to correct additive manufacturing errors in real time. For more information, please follow other related articles on the PHP Chinese website!

Hot AI Tools

Undresser.AI Undress
AI-powered app for creating realistic nude photos

AI Clothes Remover
Online AI tool for removing clothes from photos.

Undress AI Tool
Undress images for free

Clothoff.io
AI clothes remover

Video Face Swap
Swap faces in any video effortlessly with our completely free AI face swap tool!

Hot Article

Hot Tools

Notepad++7.3.1
Easy-to-use and free code editor

SublimeText3 Chinese version
Chinese version, very easy to use

Zend Studio 13.0.1
Powerful PHP integrated development environment

Dreamweaver CS6
Visual web development tools

SublimeText3 Mac version
God-level code editing software (SublimeText3)

Hot Topics


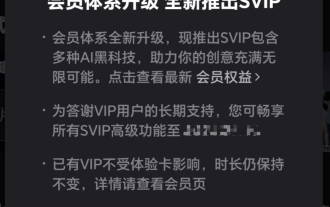
This site reported on June 27 that Jianying is a video editing software developed by FaceMeng Technology, a subsidiary of ByteDance. It relies on the Douyin platform and basically produces short video content for users of the platform. It is compatible with iOS, Android, and Windows. , MacOS and other operating systems. Jianying officially announced the upgrade of its membership system and launched a new SVIP, which includes a variety of AI black technologies, such as intelligent translation, intelligent highlighting, intelligent packaging, digital human synthesis, etc. In terms of price, the monthly fee for clipping SVIP is 79 yuan, the annual fee is 599 yuan (note on this site: equivalent to 49.9 yuan per month), the continuous monthly subscription is 59 yuan per month, and the continuous annual subscription is 499 yuan per year (equivalent to 41.6 yuan per month) . In addition, the cut official also stated that in order to improve the user experience, those who have subscribed to the original VIP
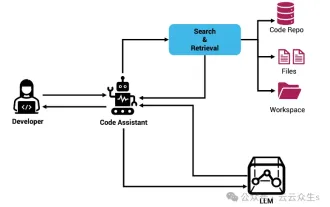
Improve developer productivity, efficiency, and accuracy by incorporating retrieval-enhanced generation and semantic memory into AI coding assistants. Translated from EnhancingAICodingAssistantswithContextUsingRAGandSEM-RAG, author JanakiramMSV. While basic AI programming assistants are naturally helpful, they often fail to provide the most relevant and correct code suggestions because they rely on a general understanding of the software language and the most common patterns of writing software. The code generated by these coding assistants is suitable for solving the problems they are responsible for solving, but often does not conform to the coding standards, conventions and styles of the individual teams. This often results in suggestions that need to be modified or refined in order for the code to be accepted into the application
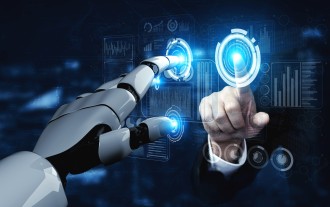
Large Language Models (LLMs) are trained on huge text databases, where they acquire large amounts of real-world knowledge. This knowledge is embedded into their parameters and can then be used when needed. The knowledge of these models is "reified" at the end of training. At the end of pre-training, the model actually stops learning. Align or fine-tune the model to learn how to leverage this knowledge and respond more naturally to user questions. But sometimes model knowledge is not enough, and although the model can access external content through RAG, it is considered beneficial to adapt the model to new domains through fine-tuning. This fine-tuning is performed using input from human annotators or other LLM creations, where the model encounters additional real-world knowledge and integrates it

To learn more about AIGC, please visit: 51CTOAI.x Community https://www.51cto.com/aigc/Translator|Jingyan Reviewer|Chonglou is different from the traditional question bank that can be seen everywhere on the Internet. These questions It requires thinking outside the box. Large Language Models (LLMs) are increasingly important in the fields of data science, generative artificial intelligence (GenAI), and artificial intelligence. These complex algorithms enhance human skills and drive efficiency and innovation in many industries, becoming the key for companies to remain competitive. LLM has a wide range of applications. It can be used in fields such as natural language processing, text generation, speech recognition and recommendation systems. By learning from large amounts of data, LLM is able to generate text
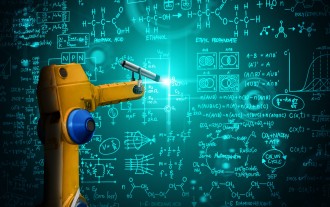
Machine learning is an important branch of artificial intelligence that gives computers the ability to learn from data and improve their capabilities without being explicitly programmed. Machine learning has a wide range of applications in various fields, from image recognition and natural language processing to recommendation systems and fraud detection, and it is changing the way we live. There are many different methods and theories in the field of machine learning, among which the five most influential methods are called the "Five Schools of Machine Learning". The five major schools are the symbolic school, the connectionist school, the evolutionary school, the Bayesian school and the analogy school. 1. Symbolism, also known as symbolism, emphasizes the use of symbols for logical reasoning and expression of knowledge. This school of thought believes that learning is a process of reverse deduction, through existing

Editor |ScienceAI Question Answering (QA) data set plays a vital role in promoting natural language processing (NLP) research. High-quality QA data sets can not only be used to fine-tune models, but also effectively evaluate the capabilities of large language models (LLM), especially the ability to understand and reason about scientific knowledge. Although there are currently many scientific QA data sets covering medicine, chemistry, biology and other fields, these data sets still have some shortcomings. First, the data form is relatively simple, most of which are multiple-choice questions. They are easy to evaluate, but limit the model's answer selection range and cannot fully test the model's ability to answer scientific questions. In contrast, open-ended Q&A
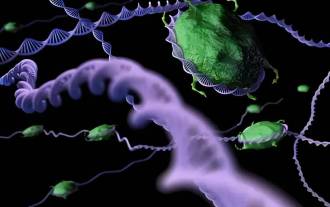
Editor | KX In the field of drug research and development, accurately and effectively predicting the binding affinity of proteins and ligands is crucial for drug screening and optimization. However, current studies do not take into account the important role of molecular surface information in protein-ligand interactions. Based on this, researchers from Xiamen University proposed a novel multi-modal feature extraction (MFE) framework, which for the first time combines information on protein surface, 3D structure and sequence, and uses a cross-attention mechanism to compare different modalities. feature alignment. Experimental results demonstrate that this method achieves state-of-the-art performance in predicting protein-ligand binding affinities. Furthermore, ablation studies demonstrate the effectiveness and necessity of protein surface information and multimodal feature alignment within this framework. Related research begins with "S
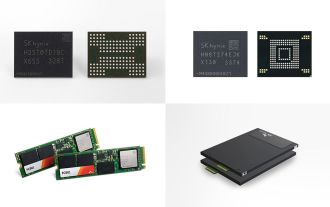
According to news from this site on August 1, SK Hynix released a blog post today (August 1), announcing that it will attend the Global Semiconductor Memory Summit FMS2024 to be held in Santa Clara, California, USA from August 6 to 8, showcasing many new technologies. generation product. Introduction to the Future Memory and Storage Summit (FutureMemoryandStorage), formerly the Flash Memory Summit (FlashMemorySummit) mainly for NAND suppliers, in the context of increasing attention to artificial intelligence technology, this year was renamed the Future Memory and Storage Summit (FutureMemoryandStorage) to invite DRAM and storage vendors and many more players. New product SK hynix launched last year
