


To control risks, the manufacturing industry uses artificial intelligence to adapt to procurement changes
With the rapid changes in the supply chain and related conditions, the procurement and sales of key materials have become a heavy burden on the shoulders of enterprises. In response to such problems, on-site procurement teams and supply chains are also promoting large-scale transformation, hoping to establish competitive advantages.
Faced with the unpredictable global economic situation, the task of multinational manufacturers is to effectively control risks, optimize digital transformation, optimize MRO (maintenance, repair, operation) expenditure analysis, and intelligently solve supplier problems The plan is incorporated into the procurement process. The purpose of these reforms is to promote a significant transformation of the procurement system and use AI technology to transform procurement plans and strategies from purely tactical actions to a new strategic decision-making model. This approach is defined by Gartner as so-called "autonomous procurement." If the measures are implemented in place, it is expected to help organizations improve their competitiveness and intelligence, and bring procurement efficiency and cost savings into a new era.
Among them, cognitive computing will contribute a force that cannot be ignored. Emerging technologies based on AI/cloud help achieve data coordination and supply chain network architecture optimization. These technologies can help procurement teams and their organizations adapt to real-world changes, ensure they are always more responsive than competitors, and strengthen partnerships with suppliers. In addition, real-time information will help organizations make more reliable data-driven decisions quickly.
But managing this kind of change is a difficult task for any technology execution team. Therefore, it is necessary for us to delve deeply into the preconditions, success factors and implementation basis of this change.
Key Strategic Change Management Principles
Let’s first look at the key change management procurement teams need to undertake when considering internal digital transformation.
Leadership Alignment – Organizations must establish flexible leadership structures. Are these managers willing to change the procurement process? Do they understand the advantages of AI technology? Can they be persuaded to embrace the coming changes?
Stakeholder involvement – Stakeholders are crucial throughout the change process. Is your team prepared to engage with the various stakeholders who will be affected by the change? For example, what is the attitude of the procurement officer or CIO? Will they be able to discuss and make decisions with you face to face?
Communication Practice - In the entire change management scenario, the team needs to conduct transparent communication based on the entire cycle. This communication must be able to address the specific needs of procurement and MRO teams, including communicating with upstream suppliers and minimizing risks.
Training and Implementation - As shown before, such large-scale change management will inevitably involve new measures and training. This training should not be a one-size-fits-all approach but should be tailored to each specific role within the procurement team.
Behavioral Adoption – The team implementing the change must be able to define metrics that help make the change more transparent to those involved.
These themes often have specific shapes in different industries and scenarios, but grasping these general principles will help companies gain broad support for change within the organization before taking action.
Using AI to Improve Operational Efficiency
A recent study by Globality shows that 90% of global procurement leaders are rapidly adapting their operating models and processes in the hope of better coping with the current turbulent and uncertain times. Real-world business challenges with certainty. Multiple data points disclosed in the study also indicate that this sign has begun to form an overall trend.
The majority of respondents (87%) are focusing on building digital and data teams, hoping to gain predictive insights and deploy new technologies to speed up response to future disruptions and economic shocks;
81% of procurement leaders believe that more support from within the enterprise is needed to achieve this critical digital transformation;
Half of the organizations surveyed expressed interest in transforming to The business procurement-centered department has shifted from simply executing routine processes to acting as a consultant and business partner.
Executives also admitted in the survey that this change in procurement and operating models will help organizations build agility and resilience in a rapidly changing business world.
Solving the labor shortage problem
The human factor in the supply chain is undoubtedly the key to promoting procurement change management. How can organizations effectively leverage human intelligence in procurement practices? Likewise, how do management teams and employees make decisions about procurement operations? The simplest answer is to introduce AI-supported technical tools.
The real challenge of labor shortage has promoted the rapid rise of AI in the field of operational manufacturing. In addition, as the baby boomer generation gradually withdraws from industrial manufacturing, fewer and fewer young people are willing to join the manufacturing and production fields. As a result, companies are more inclined to improve output efficiency through technological tools such as AI/machine learning.
For procurement managers, burnout has also become a real problem, and has even approached a disruptive "tipping point." The Ceridian 2022 Pulse of Talent survey conducted in the UK found that UK workers commonly experience some form of burnout, including deadline pressure (32%), increased workload (49%) and even mental health issues (34%).
AI tools can enhance the capabilities of human workers and eliminate this type of burnout, thereby increasing employee satisfaction. AI can take over repetitive and menial tasks that are more suitable for automation. This will not replace human jobs, but will help workers save their energy for other more strategic and fulfilling tasks. Employees can also work with management to decide how to properly use AI in a manufacturing/production environment to reduce costs and/or risks.
Real-life impact for manufacturers
Take a corporate customer as an example, a leading manufacturer of tissue, pulp, paper, sealed building products and related chemicals. The company is struggling to improve data quality as it faces poor decision-making and severe work delays due to inaccurate MRO inventory information.
The company wanted to work faster and gain more timely and accurate decision-making capabilities. To this end, they introduced data analysis, artificial intelligence and visualization tools to optimize asset strategies and inventory management levels.
The manufacturer also transitioned to new strategic management principles and overall structures for supply operations, procurement, finance and IT. By aggregating data from multiple SAP/EAM systems, AI strategies can ensure they deliver the right inventory at the right time. In just 45 days, the company also identified more than $20 million in cost savings.
Technological Change Outlook
AI technology will help procurement teams work efficiently and quickly identify and manage supplier risks. Now is the best time to streamline procurement processes, reduce costs, quickly adapt to changes, and improve compliance capabilities in response to policy/legal changes. Embracing change management and engaging in top-down communication will help your procurement team and the entire organization navigate the transition period smoothly.
The above is the detailed content of To control risks, the manufacturing industry uses artificial intelligence to adapt to procurement changes. For more information, please follow other related articles on the PHP Chinese website!

Hot AI Tools

Undresser.AI Undress
AI-powered app for creating realistic nude photos

AI Clothes Remover
Online AI tool for removing clothes from photos.

Undress AI Tool
Undress images for free

Clothoff.io
AI clothes remover

AI Hentai Generator
Generate AI Hentai for free.

Hot Article

Hot Tools

Notepad++7.3.1
Easy-to-use and free code editor

SublimeText3 Chinese version
Chinese version, very easy to use

Zend Studio 13.0.1
Powerful PHP integrated development environment

Dreamweaver CS6
Visual web development tools

SublimeText3 Mac version
God-level code editing software (SublimeText3)

Hot Topics
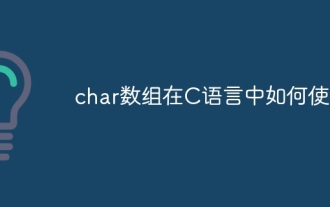
The char array stores character sequences in C language and is declared as char array_name[size]. The access element is passed through the subscript operator, and the element ends with the null terminator '\0', which represents the end point of the string. The C language provides a variety of string manipulation functions, such as strlen(), strcpy(), strcat() and strcmp().
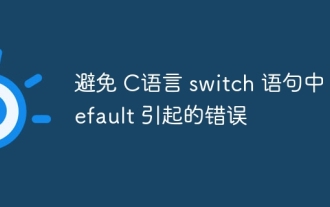
A strategy to avoid errors caused by default in C switch statements: use enums instead of constants, limiting the value of the case statement to a valid member of the enum. Use fallthrough in the last case statement to let the program continue to execute the following code. For switch statements without fallthrough, always add a default statement for error handling or provide default behavior.
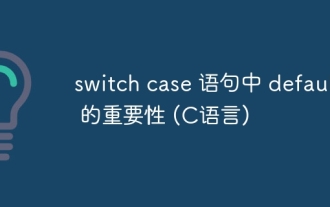
The default statement is crucial in the switch case statement because it provides a default processing path that ensures that a block of code is executed when the variable value does not match any case statement. This prevents unexpected behavior or errors and enhances the robustness of the code.
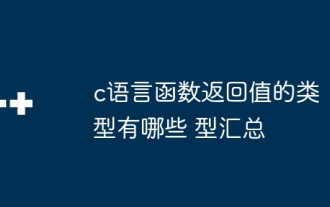
The return value types of C language function include int, float, double, char, void and pointer types. int is used to return integers, float and double are used to return floats, and char returns characters. void means that the function does not return any value. The pointer type returns the memory address, be careful to avoid memory leakage.结构体或联合体可返回多个相关数据。
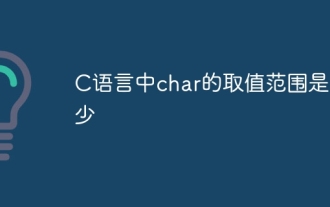
The value range of char in C language depends on the implementation method: signed char: -128 to 127 Unsigned char: 0 to 255 The specific range is affected by computer architecture and compiler options. By default, char is set to a signed type.
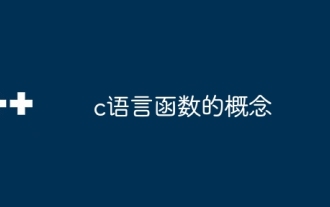
C language functions are reusable code blocks. They receive input, perform operations, and return results, which modularly improves reusability and reduces complexity. The internal mechanism of the function includes parameter passing, function execution, and return values. The entire process involves optimization such as function inline. A good function is written following the principle of single responsibility, small number of parameters, naming specifications, and error handling. Pointers combined with functions can achieve more powerful functions, such as modifying external variable values. Function pointers pass functions as parameters or store addresses, and are used to implement dynamic calls to functions. Understanding function features and techniques is the key to writing efficient, maintainable, and easy to understand C programs.
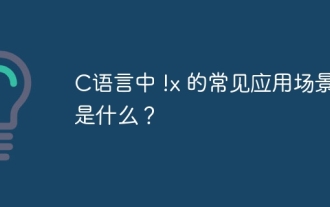
The purpose of !x in C language is not limited to inverse: logical judgment: whether it is 0 is more concise than x == 0. Control program flow or represent status: use 0 and non-0 to represent true or false. Bit operation: Quickly invert all bits (use with caution).
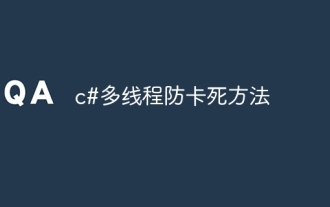
The following ways to avoid "stuck" multithreading in C#: avoid time-consuming operations on UI threads. Use Task and async/await to perform time-consuming operations asynchronously. Update the UI on the UI thread via Application.Current.Dispatcher.Invoke. Use the CancellationToken to control task cancellation. Make rational use of thread pools to avoid excessive creation of threads. Pay attention to code readability and maintainability, making it easy to debug. Logs are recorded in each thread for easy debugging.
