Artificial intelligence: the driver of Industry 4.0
A lot of the hype surrounding artificial intelligence in manufacturing focuses on industrial automation, but that’s just intelligence An aspect of the factory revolution—a natural next step in the quest for efficiency. Artificial intelligence also brings the ability to reveal new business avenues for manufacturing tables. As part of the emerging Industry 4.0 paradigm, we will provide an overview of AI’s ability to drive industrial automation and open up new business opportunities. Additionally, we'll cover how manufacturers can use this powerful technology to increase efficiency, improve quality, and better manage their supply chains.
Artificial Intelligence Manufacturing Use Cases
#1: Predicting Quality and Yield
Reducing production losses and preventing inefficiencies in the production process have always been a priority for manufacturers across all industries challenges faced. This is as true today as ever-increasing demand meets increasing competition.
On the one hand, consumer expectations are high; global consumption habits are gradually "Westernizing" even as the population surge continues. According to multiple surveys in recent years, the global population will grow by 25% by 2050, equivalent to 200,000 new mouths every day.
On the other hand, consumers have never had so many products to choose from. Recent surveys suggest that this abundance of choice means consumers are increasingly likely to abandon their favorite brands permanently, for example, if the product is no longer on the shelf.
Given these trends, manufacturers can no longer accept process inefficiencies and their associated losses. Every loss in waste, yield, quality or throughput erodes their bottom line and gives competitors an extra inch - assuming their production processes are more efficient.
The challenge faced by many manufacturers, especially those with complex processes, is that they eventually hit a ceiling when it comes to process optimization. Some inefficiencies have no obvious root cause, leaving process experts unable to explain them.
Predict Quality and Yield uses AI-driven process and machine health solutions to uncover the hidden causes of many of the perennial production losses manufacturers face. This is accomplished through continuous multivariate analysis, using uniquely trained machine learning algorithms to gain insights into individual production processes.
The specific artificial intelligence/machine learning technique used here is called supervised learning, which means the algorithm is trained to identify trends and patterns in data. Automated recommendations and alerts can then be generated to notify production teams and process engineers of impending issues and seamlessly share critical knowledge on how to prevent losses before they occur.
#2: Predictive maintenance
Predictive maintenance is one of the most famous applications of industrial artificial intelligence. Rather than performing maintenance according to a predetermined schedule, predictive maintenance uses algorithms to predict the next failure of a component, machine or system and then alerts personnel to perform focused maintenance procedures to prevent failure. These alerts occur at the right time to avoid unnecessary downtime.
These maintenance systems rely on unsupervised machine learning techniques to formulate predictions. Predictive maintenance solutions can help reduce costs while, in many cases, eliminating the need for planned downtime, thereby strengthening the bottom line and improving the employee experience.
With machine learning preventing failures, systems can continue to operate without unnecessary interruptions or delays. The required maintenance is very specific - technicians are informed of the components that need to be inspected, repaired and replaced; which tools to use and which methods to follow.
Predictive maintenance can also extend the remaining useful life (RUL) of machines and equipment, as secondary damage can be prevented while requiring less labor to perform maintenance procedures. Improving RUL can increase sustainability efforts and reduce waste.
#3: Human-robot collaboration
According to the International Federation of Robotics (IFR), as of 2020, there were approximately 1.64 million industrial robots in operation around the world. There are fears that robots will take away jobs, but the industry is seeing workers embrace programming, design, and maintenance.
Humans also work alongside robots to improve efficiency and productivity on and off the factory floor. As robots become more entrenched in manufacturing, artificial intelligence will play an important role. It will ensure the safety of human workers and give robots more autonomy to make decisions that can further optimize processes based on real-time data collected from the production floor.
#4: Generative Design
Manufacturers can also leverage artificial intelligence during the design phase. With a well-defined design brief as input, designers and engineers can use AI algorithms (often called generative design software) to explore all possible configurations of a solution.
The briefing can include limitations and definitions of material types, production methods, time constraints and budget constraints. The set of solutions generated by the algorithm can then be tested using machine learning. The testing phase provides additional information about which ideas or design decisions work and which don’t. From there, additional improvements can be made until an optimal solution is reached.
#5: Market Adaptation and Supply Chain
Artificial intelligence permeates the entire Industry 4.0 ecosystem and is not limited to the production workshop. Artificial intelligence algorithms can optimize the supply chain of manufacturing operations, helping manufacturers better respond to and predict changing markets.
Algorithms can construct market demand estimates by considering demand patterns categorized by various factors such as date, location, socio-economic attributes, macroeconomic behavior, political status, weather patterns, etc. Manufacturers can use this information to plan the path forward. Some of the processes that can be optimized using these insights include inventory control, staffing, energy consumption, raw materials, and financial decisions.
Industry 4.0 and Collaboration
AI is popular, but it requires collaboration to be used correctly. First, manufacturers should weigh the pros and cons of buying versus building the technology and expertise required. An Industry 4.0 system consists of many elements and stages that are unique to manufacturers:
- Historical data collection.
- Capture real-time data through sensors.
- Data aggregation.
- Connect through communication protocols, routing and gateway devices.
- Integrate with PLC.
- Dashboard for monitoring and analysis.
- Artificial Intelligence Applications: Machine Learning and Other Technologies.
Industrial artificial intelligence is no longer a distant aspiration. Manufacturers can now use these technologies to address their specific business challenges and needs. As Industry 4.0 evolves and becomes more complex, manufacturers will need the agility and visibility that AI brings.
The above is the detailed content of Artificial intelligence: the driver of Industry 4.0. For more information, please follow other related articles on the PHP Chinese website!

Hot AI Tools

Undresser.AI Undress
AI-powered app for creating realistic nude photos

AI Clothes Remover
Online AI tool for removing clothes from photos.

Undress AI Tool
Undress images for free

Clothoff.io
AI clothes remover

AI Hentai Generator
Generate AI Hentai for free.

Hot Article

Hot Tools

Notepad++7.3.1
Easy-to-use and free code editor

SublimeText3 Chinese version
Chinese version, very easy to use

Zend Studio 13.0.1
Powerful PHP integrated development environment

Dreamweaver CS6
Visual web development tools

SublimeText3 Mac version
God-level code editing software (SublimeText3)

Hot Topics
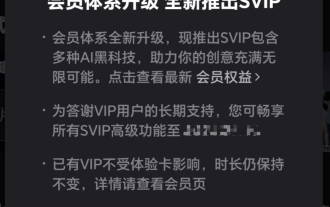
This site reported on June 27 that Jianying is a video editing software developed by FaceMeng Technology, a subsidiary of ByteDance. It relies on the Douyin platform and basically produces short video content for users of the platform. It is compatible with iOS, Android, and Windows. , MacOS and other operating systems. Jianying officially announced the upgrade of its membership system and launched a new SVIP, which includes a variety of AI black technologies, such as intelligent translation, intelligent highlighting, intelligent packaging, digital human synthesis, etc. In terms of price, the monthly fee for clipping SVIP is 79 yuan, the annual fee is 599 yuan (note on this site: equivalent to 49.9 yuan per month), the continuous monthly subscription is 59 yuan per month, and the continuous annual subscription is 499 yuan per year (equivalent to 41.6 yuan per month) . In addition, the cut official also stated that in order to improve the user experience, those who have subscribed to the original VIP
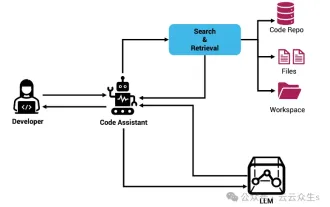
Improve developer productivity, efficiency, and accuracy by incorporating retrieval-enhanced generation and semantic memory into AI coding assistants. Translated from EnhancingAICodingAssistantswithContextUsingRAGandSEM-RAG, author JanakiramMSV. While basic AI programming assistants are naturally helpful, they often fail to provide the most relevant and correct code suggestions because they rely on a general understanding of the software language and the most common patterns of writing software. The code generated by these coding assistants is suitable for solving the problems they are responsible for solving, but often does not conform to the coding standards, conventions and styles of the individual teams. This often results in suggestions that need to be modified or refined in order for the code to be accepted into the application

To learn more about AIGC, please visit: 51CTOAI.x Community https://www.51cto.com/aigc/Translator|Jingyan Reviewer|Chonglou is different from the traditional question bank that can be seen everywhere on the Internet. These questions It requires thinking outside the box. Large Language Models (LLMs) are increasingly important in the fields of data science, generative artificial intelligence (GenAI), and artificial intelligence. These complex algorithms enhance human skills and drive efficiency and innovation in many industries, becoming the key for companies to remain competitive. LLM has a wide range of applications. It can be used in fields such as natural language processing, text generation, speech recognition and recommendation systems. By learning from large amounts of data, LLM is able to generate text
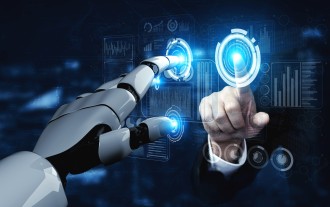
Large Language Models (LLMs) are trained on huge text databases, where they acquire large amounts of real-world knowledge. This knowledge is embedded into their parameters and can then be used when needed. The knowledge of these models is "reified" at the end of training. At the end of pre-training, the model actually stops learning. Align or fine-tune the model to learn how to leverage this knowledge and respond more naturally to user questions. But sometimes model knowledge is not enough, and although the model can access external content through RAG, it is considered beneficial to adapt the model to new domains through fine-tuning. This fine-tuning is performed using input from human annotators or other LLM creations, where the model encounters additional real-world knowledge and integrates it

Editor |ScienceAI Question Answering (QA) data set plays a vital role in promoting natural language processing (NLP) research. High-quality QA data sets can not only be used to fine-tune models, but also effectively evaluate the capabilities of large language models (LLM), especially the ability to understand and reason about scientific knowledge. Although there are currently many scientific QA data sets covering medicine, chemistry, biology and other fields, these data sets still have some shortcomings. First, the data form is relatively simple, most of which are multiple-choice questions. They are easy to evaluate, but limit the model's answer selection range and cannot fully test the model's ability to answer scientific questions. In contrast, open-ended Q&A
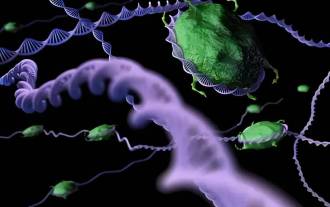
Editor | KX In the field of drug research and development, accurately and effectively predicting the binding affinity of proteins and ligands is crucial for drug screening and optimization. However, current studies do not take into account the important role of molecular surface information in protein-ligand interactions. Based on this, researchers from Xiamen University proposed a novel multi-modal feature extraction (MFE) framework, which for the first time combines information on protein surface, 3D structure and sequence, and uses a cross-attention mechanism to compare different modalities. feature alignment. Experimental results demonstrate that this method achieves state-of-the-art performance in predicting protein-ligand binding affinities. Furthermore, ablation studies demonstrate the effectiveness and necessity of protein surface information and multimodal feature alignment within this framework. Related research begins with "S
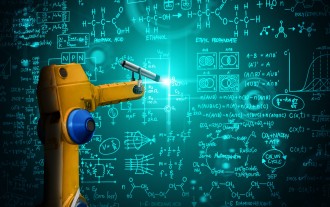
Machine learning is an important branch of artificial intelligence that gives computers the ability to learn from data and improve their capabilities without being explicitly programmed. Machine learning has a wide range of applications in various fields, from image recognition and natural language processing to recommendation systems and fraud detection, and it is changing the way we live. There are many different methods and theories in the field of machine learning, among which the five most influential methods are called the "Five Schools of Machine Learning". The five major schools are the symbolic school, the connectionist school, the evolutionary school, the Bayesian school and the analogy school. 1. Symbolism, also known as symbolism, emphasizes the use of symbols for logical reasoning and expression of knowledge. This school of thought believes that learning is a process of reverse deduction, through existing
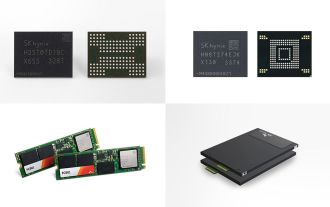
According to news from this site on August 1, SK Hynix released a blog post today (August 1), announcing that it will attend the Global Semiconductor Memory Summit FMS2024 to be held in Santa Clara, California, USA from August 6 to 8, showcasing many new technologies. generation product. Introduction to the Future Memory and Storage Summit (FutureMemoryandStorage), formerly the Flash Memory Summit (FlashMemorySummit) mainly for NAND suppliers, in the context of increasing attention to artificial intelligence technology, this year was renamed the Future Memory and Storage Summit (FutureMemoryandStorage) to invite DRAM and storage vendors and many more players. New product SK hynix launched last year
