


What are the benefits of achieving real-time manufacturing visibility?
Dealing with the impact of the global recession, while dealing with ongoing supply chain disruptions, labor shortages and rising energy costs, is forcing manufacturing companies to explore innovative ways to address business challenges.
Seeking to improve operational efficiency, ensure long-term growth and stay ahead of the competition, manufacturers are investing more in digital technologies such as MES, SCADA/HMI, predictive maintenance, simulation/digital twins, and edge-to-cloud . Manufacturing will benefit from the additional data these technologies bring, providing deeper insights for operational improvements.
Many manufacturers believe that increased capital investment is critical to improving productivity, especially in the process of increasing production capacity, improving quality and reducing costs. Manufacturers will invest more in software, acquisitions, new equipment and international expansion as they seek to achieve broader growth goals, accelerate digitalization, transition to net zero and open up new global markets.
Despite the current uncertainty, manufacturers recognize that investment is critical to boost growth, increase productivity and remain competitive in the global marketplace. It’s no secret that the manufacturing landscape is changing rapidly, and tomorrow’s manufacturing leaders need to stay ahead of the game today. Demand for new products and shortened delivery times show no signs of slowing down, with customer relationships reliant on fast, efficient “on-demand” delivery.
World-class manufacturers measure and monitor an agreed-upon set of KPIs and use them to evaluate business performance and as input to decision-making. Traditional metrics such as overall equipment efficiency and downtime are effective but have limitations when assessing overall manufacturing efficiency and productivity. Driving continuous improvement throughout the manufacturing process requires additional KPI metrics that take into account all areas that impact productivity, thereby increasing visibility.
1. Leverage real-time data to make actionable improvements
Measuring OEE is an important part of implementing digital lean and performance improvement initiatives. The data provided in the performance system must be processed quickly, otherwise, production managers will have difficulty discovering the root cause of the problem. Shop floor teams are encouraged to use data to uncover the causes of process inefficiencies to drive improvements, creating a culture of continuous improvement as operators actively engage with the system and see the value derived from it.
2. Ensure regulatory compliance and quality
Real-time visibility into quality issues, such as non-compliance events or process out-of-control, is critical to increasing yields, reducing production waste and avoiding costly Product recalls are critical. The impact of a product recall on a brand's reputation can be huge and the associated costs/hefty fines can be huge, not just for production. Understanding process capabilities across a manufacturing facility is critical to reducing low-quality costs, promoting continuous improvement, and creating sustainable competitive advantage.
3. Manage Energy Consumption
As energy costs continue to rise to unprecedented levels and energy contracts are about to expire, business owners will be concerned about how to manage rising energy bills. and reduce energy consumption. Measure and monitor energy usage in real time, rather than through monthly or quarterly energy bills, allowing for comprehensive corrective action.
Additionally, help proactively reduce energy by integrating energy and production data to identify improvement opportunities! Not forgetting the importance of achieving long-term sustainability and carbon reduction targets is another benefit of implementing digital technologies to support energy reduction targets.
4. Reduce production losses
Availability losses such as planned or unplanned downtime, machine installation time, inventory turnover and changeover time, will have a negative impact on OEE and performance . However, aspects such as the impact of non-productive tasks, machine downtime and its impact on other production are difficult to capture. Identifying inefficiencies throughout the production process is key to providing the real-time information needed to take corrective action.
5. Optimize maintenance activities
Unscheduled maintenance will lead to production losses, increased parts costs and time loss to repair problems, and the cost is significantly higher than planned maintenance. Adopt a more proactive approach to preventive maintenance to coincide with planned production downtime, significantly reducing costs.
Preventive maintenance needs to be effectively controlled and managed to ensure that equipment continues to produce high-quality products. Visibility into equipment availability and performance can help reduce unplanned downtime, optimize maintenance activities and get the most value from your assets.
6. Understand Labor Costs
Having the right number of people and a balance of skills on the shop floor is a huge juggling act! Too little can create bottlenecks and lead to missed production deadlines, too much can cause unnecessary labor costs and impact profits.
Obtaining detailed workforce information, such as how many employees are needed on a production line, required skill sets, and how long it takes to complete a job, will help paint a picture of your workforce needs. Likewise, understanding the relationship between employee performance and output, how profitable work is being run, and understanding the true cost of labor are also important considerations when optimizing workforce performance and ensuring maximum productivity.
7. Reduce Goods Cost
Most manufacturers include direct materials, labor and overhead when estimating costs. Here are three things to understand when trying to reduce your cost of goods, which can help achieve your business's bottom-line KPIs, including improving profit margins, ensuring business sustainability, and improving customer satisfaction. Increased visibility through digital technology and real-time data analytics can reduce cost of goods.
The above is the detailed content of What are the benefits of achieving real-time manufacturing visibility?. For more information, please follow other related articles on the PHP Chinese website!

Hot AI Tools

Undresser.AI Undress
AI-powered app for creating realistic nude photos

AI Clothes Remover
Online AI tool for removing clothes from photos.

Undress AI Tool
Undress images for free

Clothoff.io
AI clothes remover

AI Hentai Generator
Generate AI Hentai for free.

Hot Article

Hot Tools

Notepad++7.3.1
Easy-to-use and free code editor

SublimeText3 Chinese version
Chinese version, very easy to use

Zend Studio 13.0.1
Powerful PHP integrated development environment

Dreamweaver CS6
Visual web development tools

SublimeText3 Mac version
God-level code editing software (SublimeText3)

Hot Topics


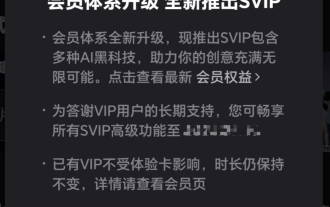
This site reported on June 27 that Jianying is a video editing software developed by FaceMeng Technology, a subsidiary of ByteDance. It relies on the Douyin platform and basically produces short video content for users of the platform. It is compatible with iOS, Android, and Windows. , MacOS and other operating systems. Jianying officially announced the upgrade of its membership system and launched a new SVIP, which includes a variety of AI black technologies, such as intelligent translation, intelligent highlighting, intelligent packaging, digital human synthesis, etc. In terms of price, the monthly fee for clipping SVIP is 79 yuan, the annual fee is 599 yuan (note on this site: equivalent to 49.9 yuan per month), the continuous monthly subscription is 59 yuan per month, and the continuous annual subscription is 499 yuan per year (equivalent to 41.6 yuan per month) . In addition, the cut official also stated that in order to improve the user experience, those who have subscribed to the original VIP
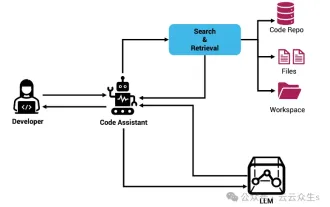
Improve developer productivity, efficiency, and accuracy by incorporating retrieval-enhanced generation and semantic memory into AI coding assistants. Translated from EnhancingAICodingAssistantswithContextUsingRAGandSEM-RAG, author JanakiramMSV. While basic AI programming assistants are naturally helpful, they often fail to provide the most relevant and correct code suggestions because they rely on a general understanding of the software language and the most common patterns of writing software. The code generated by these coding assistants is suitable for solving the problems they are responsible for solving, but often does not conform to the coding standards, conventions and styles of the individual teams. This often results in suggestions that need to be modified or refined in order for the code to be accepted into the application
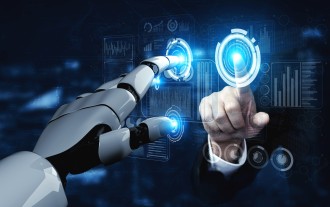
Large Language Models (LLMs) are trained on huge text databases, where they acquire large amounts of real-world knowledge. This knowledge is embedded into their parameters and can then be used when needed. The knowledge of these models is "reified" at the end of training. At the end of pre-training, the model actually stops learning. Align or fine-tune the model to learn how to leverage this knowledge and respond more naturally to user questions. But sometimes model knowledge is not enough, and although the model can access external content through RAG, it is considered beneficial to adapt the model to new domains through fine-tuning. This fine-tuning is performed using input from human annotators or other LLM creations, where the model encounters additional real-world knowledge and integrates it

To learn more about AIGC, please visit: 51CTOAI.x Community https://www.51cto.com/aigc/Translator|Jingyan Reviewer|Chonglou is different from the traditional question bank that can be seen everywhere on the Internet. These questions It requires thinking outside the box. Large Language Models (LLMs) are increasingly important in the fields of data science, generative artificial intelligence (GenAI), and artificial intelligence. These complex algorithms enhance human skills and drive efficiency and innovation in many industries, becoming the key for companies to remain competitive. LLM has a wide range of applications. It can be used in fields such as natural language processing, text generation, speech recognition and recommendation systems. By learning from large amounts of data, LLM is able to generate text
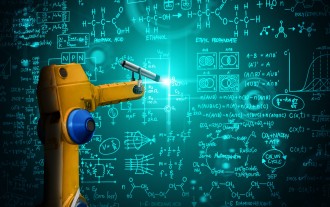
Machine learning is an important branch of artificial intelligence that gives computers the ability to learn from data and improve their capabilities without being explicitly programmed. Machine learning has a wide range of applications in various fields, from image recognition and natural language processing to recommendation systems and fraud detection, and it is changing the way we live. There are many different methods and theories in the field of machine learning, among which the five most influential methods are called the "Five Schools of Machine Learning". The five major schools are the symbolic school, the connectionist school, the evolutionary school, the Bayesian school and the analogy school. 1. Symbolism, also known as symbolism, emphasizes the use of symbols for logical reasoning and expression of knowledge. This school of thought believes that learning is a process of reverse deduction, through existing

Editor |ScienceAI Question Answering (QA) data set plays a vital role in promoting natural language processing (NLP) research. High-quality QA data sets can not only be used to fine-tune models, but also effectively evaluate the capabilities of large language models (LLM), especially the ability to understand and reason about scientific knowledge. Although there are currently many scientific QA data sets covering medicine, chemistry, biology and other fields, these data sets still have some shortcomings. First, the data form is relatively simple, most of which are multiple-choice questions. They are easy to evaluate, but limit the model's answer selection range and cannot fully test the model's ability to answer scientific questions. In contrast, open-ended Q&A
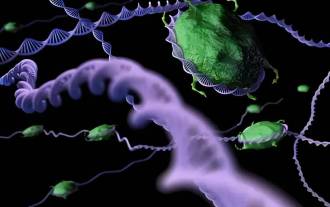
Editor | KX In the field of drug research and development, accurately and effectively predicting the binding affinity of proteins and ligands is crucial for drug screening and optimization. However, current studies do not take into account the important role of molecular surface information in protein-ligand interactions. Based on this, researchers from Xiamen University proposed a novel multi-modal feature extraction (MFE) framework, which for the first time combines information on protein surface, 3D structure and sequence, and uses a cross-attention mechanism to compare different modalities. feature alignment. Experimental results demonstrate that this method achieves state-of-the-art performance in predicting protein-ligand binding affinities. Furthermore, ablation studies demonstrate the effectiveness and necessity of protein surface information and multimodal feature alignment within this framework. Related research begins with "S
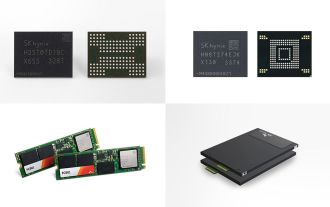
According to news from this site on August 1, SK Hynix released a blog post today (August 1), announcing that it will attend the Global Semiconductor Memory Summit FMS2024 to be held in Santa Clara, California, USA from August 6 to 8, showcasing many new technologies. generation product. Introduction to the Future Memory and Storage Summit (FutureMemoryandStorage), formerly the Flash Memory Summit (FlashMemorySummit) mainly for NAND suppliers, in the context of increasing attention to artificial intelligence technology, this year was renamed the Future Memory and Storage Summit (FutureMemoryandStorage) to invite DRAM and storage vendors and many more players. New product SK hynix launched last year
