What hardware does machine vision contain?
As various industries begin to have widespread demands for industrial automation and intelligence using image and machine vision technology, machine vision has gradually begun to be applied in industrial sites.
Driven by the government’s favorable policies, the domestic machine vision industry is developing rapidly, and China is becoming one of the most active regions in the world for machine vision development. It is expected that the size of my country's machine vision market will reach 24.6 billion yuan by 2025. Let’s take a deeper look at machine vision.
Machine vision is a comprehensive technology, including image processing, mechanical engineering technology, control, electric light source lighting, optical imaging, sensors, analog and digital video technology, computer software and hardware technology (image enhancement and analysis algorithms, Image card, I/O card, etc.).
A typical machine vision application system includes image capture, light source system, image digitization module, digital image processing module, intelligent judgment and decision-making module and mechanical control execution module.
In general, machine vision is a comprehensive technology that combines software and hardware. It requires software to process images and hardware to provide stable and high-quality images. Both are equally important. As a developer, I am relatively familiar with software modules and have a weaker knowledge base on hardware systems. This article provides a simple summary of hardware-related resources in machine vision. Interested friends may wish to refer to it.
Summary of content:
1. Industrial computer
The industrial computer can be understood as a PC host, but this host is very important in image acquisition and processing and related The controls and interfaces are made stronger. In the machine vision system, the performance of the industrial computer directly affects the processing speed and running time of the entire vision system, and is the key to the entire vision system. The selection of industrial computer needs to consider the following 4 aspects:
1) Size
2) Installation method
3) Configuration
---- --Just choose the appropriate configuration according to your application.
4) Interface
-------It is very important to determine the number of cameras, light source controllers and connection methods in the vision system. For example, the system has 8 cameras and 4 light sources need to be controlled. The cameras are connected through network cables and the light source controller is a 232 interface. This way the number of network interfaces and serial ports of the industrial computer can be determined.
2. Camera
2.1 Camera type
Point array camera/area array camera
Area Array camera: It implements pixel matrix shooting. In images captured by a camera, the details of the image are not determined by the number of pixels, but by the resolution. The resolution is determined by the focal length of the selected lens. For the same camera, the resolution will be different if lenses with different focal lengths are used. The number of pixels does not determine the resolution (sharpness) of the image, so what are the benefits of a camera with large pixels? There is only one answer: reduce the number of shots and increase the test speed.
Line scan camera: As the name suggests, it is in the shape of a "line". Although it is also a two-dimensional image, it is extremely long. The length is several K, but the width is only a few pixels. Generally, this kind of camera is only used in two situations: 1. The field of view to be measured is an elongated strip, which is mostly used for inspection problems on rollers.
2. Requires a huge field of view or extremely high precision. In the second case (requiring a huge field of view or extremely high precision), it is necessary to use an excitation device to excite the camera multiple times, take multiple photos, and then merge the multiple "bar"-shaped images captured. into a huge picture.
Therefore, when using a line array camera, you must use a capture card that can support the line array camera. Line array cameras are expensive, and in the case of large field of view or high-precision detection, their detection speed is also slow - the image of a general camera is 400K ~ 1M, and the combined image is several M as large, and the speed Naturally it is slower. Slow work leads to fine work. For these two reasons, line scan cameras are only used in very special circumstances.
CCD Camera/CMOS Camera
CCD camera can provide good image quality and anti-noise capability, although the size of the system becomes larger due to the addition of external circuits. It can be improved by copying, but the circuit designer can be more flexible and better improve the performance of some special concerns of CCD cameras. CCD is more suitable for applications that require very high camera performance but less stringent cost control, such as astronomy, high-definition medical X-ray images, and other applications that require long-term exposure and have strict requirements on image noise.
CMOS cameras have the advantages of high yield, high integration, low power consumption, and low price. But the image itself has a lot of noise. The current CMOS technology continues to develop, has overcome many of its early shortcomings, and has developed to a level that can compete with CCD technology in terms of image quality.
CMOS is suitable for applications that require small space, small volume, and low power consumption but do not have particularly high image noise and quality requirements. Such as most auxiliary lighting industrial inspection applications, security applications, and most consumer commercial digital cameras. At present, CCD industrial cameras still occupy a dominant position in visual inspection solutions.
2.2 Resolution
The number of pixels each time the camera collects an image generally corresponds to the number of pixels arranged on the target surface of the photoelectric sensor. The choice of resolution also needs to be determined based on the usage scenario and accuracy requirements. Higher is not better.
2.3 Pixel depth
The number of bits per pixel data, the common ones are 8bit, 10bit, and 12bit. Resolution and pixel depth together determine the size of the image. For example, for 5 million pixels with a pixel depth of 8bit, the entire picture should be 5 million*8/1024/1024=37M (1024Byte=1KB, 1024KB=1M). Increasing pixel depth can enhance measurement accuracy, but it also slows down the system and makes system integration more difficult (increased cables, larger size, etc.).
2.4 Frame rate
The speed at which the camera collects and transmits images. For area array cameras, it is generally the number of frames collected per second (Frames/Sec). For line array cameras, it is generally the number of frames collected per second (Frames/Sec). The camera captures the number of lines per second (HZ). The choice of frame rate needs to take into account the dynamic scene being captured.
2.5 Exposure
Industrial line scan cameras are line-by-line exposure methods. You can choose fixed line frequency and external trigger synchronization. The exposure time can be adjusted with the line period. consistent, or you can set a fixed time; area scan cameras have several common methods: frame exposure, field exposure and rolling exposure. Industrial digital cameras generally provide the function of external trigger acquisition, and the shutter speed can generally reach 10ms. High-speed cameras It will be faster.
2.6 Noise
Noise refers to signals outside the actual imaging target that are not expected to be collected during the imaging process. Generally speaking, it is divided into two categories. One is the shot noise caused by the effective signal, which exists for any camera; the other is the noise inherent in the camera itself and has nothing to do with the signal. It is due to the inherent noise caused by the image sensor readout circuit, camera signal processing and amplification circuit. The inherent noise of each camera is different.
2.7 Development interface
For the development of visual projects using cameras, camera control (photography, video recording, saving, setting parameters, etc.) is essential , generally manufacturers will provide control demos, and the control functions need to be applied to our projects during development.
3. Lens
Cameras and lenses are generally matched. The lens selection mainly considers the viewing distance of the image. The lens selection steps are:
1) Calculate the short distance The number of pixels corresponding to the side E=B/C, the number of pixels on the long side and short side of the camera must be greater than E;
2) Pixel size = product short side size B/short side pixels of the selected camera Number
3) Magnification = short film size of the selected camera chip/field of view range of the short side of the camera
4) Resolvable product accuracy = pixel size/magnification (determine whether it is smaller than C )
5) Focal length of objective lens = working distance/(1 1/magnification) Unit: mm
6) The resolution of the image plane must be greater than 1/(2×0.1×magnification ) Unit: lp/mm
The CCD size of the selected lens must be greater than or equal to the size of the camera's CCD sensor chip. In addition, whether the mounting base is a C, CS or F-type interface must also match, and the working distance of the lens must also be considered. , whether there is enough space, etc. If you are still unsure about the choice of lens, you can consult the manufacturer's technical support and let the manufacturer recommend a suitable lens based on your application scenario.
4. Light source
Filling light is a necessary operation in machine vision. If you simply increase the exposure time of the camera, it will increase the noise of the image and reduce the quality of the image. You must choose A suitable light source will do. The selection of light source is divided into two parts: light source lamp and light source controller.
4.1 Light source lamp
Machine vision also provides a wide range of light sources. This is because the vision industry is widely used and it is necessary to choose the appropriate light source according to the specific project. will achieve the desired effect.
Common types of light source lamps are as follows, which can be selected according to specific projects.
4.2 Light source controller
The light source controller is for the test environment Those who provide lighting will generally provide a development interface to control the designated output port to light up or turn off, mainly to cooperate with the camera to provide the software with images that meet the requirements.
5. Physical environment
The machine vision system has relatively high requirements for the test environment, involving issues such as cameras, light sources, and placement of the target to be tested. The principle is to provide a stable, high-performance quality images. The test environment may also need to be designed by a professional organization. If it is a simple environment for experiments, you can purchase experimental brackets online.
The above is the detailed content of What hardware does machine vision contain?. For more information, please follow other related articles on the PHP Chinese website!

Hot AI Tools

Undresser.AI Undress
AI-powered app for creating realistic nude photos

AI Clothes Remover
Online AI tool for removing clothes from photos.

Undress AI Tool
Undress images for free

Clothoff.io
AI clothes remover

AI Hentai Generator
Generate AI Hentai for free.

Hot Article

Hot Tools

Notepad++7.3.1
Easy-to-use and free code editor

SublimeText3 Chinese version
Chinese version, very easy to use

Zend Studio 13.0.1
Powerful PHP integrated development environment

Dreamweaver CS6
Visual web development tools

SublimeText3 Mac version
God-level code editing software (SublimeText3)

Hot Topics



As various industries begin to have widespread demands for industrial automation and intelligence using image and machine vision technology, machine vision has gradually begun to be applied in industrial sites. Driven by the government's favorable policies, the domestic machine vision industry is developing rapidly, and China is becoming one of the most active regions in the world for machine vision development. It is expected that the size of my country's machine vision market will reach 24.6 billion yuan by 2025. Let’s take a deeper look at machine vision. Machine vision is a comprehensive technology, including image processing, mechanical engineering technology, control, electric light source lighting, optical imaging, sensors, analog and digital video technology, computer software and hardware technology (image enhancement and analysis algorithms, image cards, I/O card, etc.). A typical machine vision application system includes image capture, light source system, image

Following the popularity of GroundedSAM, the IDEA Research Institute team returns with a new work: the new visual prompt (VisualPrompt) model T-Rex, which uses pictures to recognize pictures and can be used right out of the box, opening up a new world of open set detection! Pull the frame, check and complete! At the just-concluded 2023 IDEA conference, Shen Xiangyang, founding chairman of the IDEA Research Institute and foreign academician of the National Academy of Engineering, demonstrated a new target detection experience based on visual cues and released the model laboratory (playground) of the new visual cues model T-Rex ), InteractiveVisualPrompt (iVP), which set off a wave of trial climaxes on site. On iVP, users can personally unlock “a
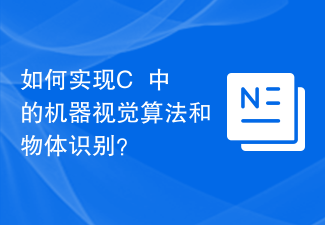
How to implement machine vision algorithms and object recognition in C++? Introduction: With the continuous development and application of artificial intelligence, machine vision technology has been widely used in various fields, such as autonomous driving, security monitoring, medical imaging, etc. Among them, C++, as a widely used programming language, has the characteristics of high compilation efficiency and strong flexibility, and has gradually become the preferred language for the implementation of machine vision algorithms. This article will introduce how to implement machine vision algorithms and object recognition through C++, and attach code examples. I hope it can provide some help to readers.
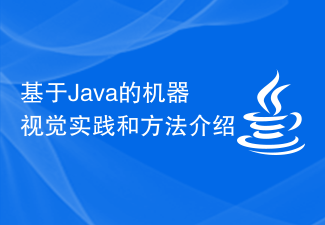
With the continuous development of science and technology, machine vision technology has been widely used in various fields, such as industrial automation, medical diagnosis, security monitoring, etc. As a popular programming language, Java also has important applications in the field of machine vision. This article will introduce Java-based machine vision practices and related methods. 1. Application of Java in machine vision As a cross-platform programming language, Java has the advantages of cross-operating systems, easy maintenance, and high scalability. It has certain advantages for machine vision applications. Java

Over the past few years, the use of Go language has gradually increased in many different fields, including machine vision and pattern recognition. Go language is widely popular for its concurrency, simplicity and ease of use. This article will explore the advantages of using Go language in machine vision and pattern recognition and how to use Go to implement these applications. Advantages of Go Concurrency The concurrency of Go language is one of its greatest advantages. Compared with other languages, Go can easily achieve efficient concurrent processing. This has applications in machine vision and pattern recognition
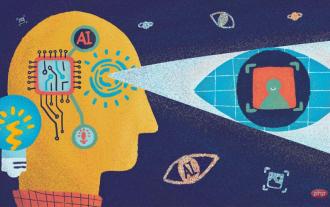
Machine Vision is a combination of hardware and software used in industrial and non-industrial fields. Its main function is to capture and process images and provide operational guidance for equipment execution. It is a pioneering force in intelligent manufacturing and is mainly used in manufacturing. Front-end links such as electronics manufacturing and automobiles. Machine Vision The domestic machine vision industry started in the 1990s. It initially represented foreign machine vision products. After entering the 21st century, a few local machine vision companies gradually started independent research and development. According to CBInsight data, China is currently the third largest machine vision application market after the United States and Japan. Including machine vision equipment, the localization rate is about 40%. It is expected that the localization rate will increase to 55% in 2022.
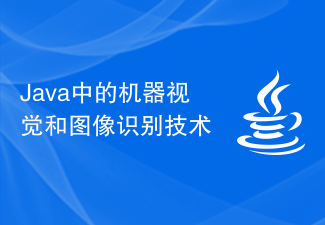
Java is currently one of the most widely used programming languages in the world, and machine vision and image recognition technology are one of the areas that have attracted much attention in recent years. This article will explore how to use Java to implement machine vision and image recognition technology, and introduce the theoretical basis and practical applications. 1. Introduction to machine vision and image recognition technology Machine vision and image recognition technology refers to converting images into digital signals through computers and digital signal processing technology, and performing digital processing and analysis on them, ultimately achieving automatic recognition and analysis of images. . it
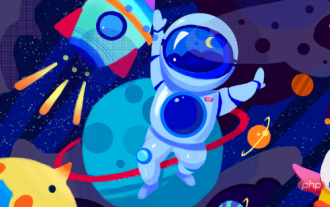
Machine vision (MV) uses technology that enables industrial machines to "see" and analyze tasks and make quick decisions based on what the system sees. MV is quickly becoming one of the most core technologies in automation. Given that this technology is now being merged with machine learning (ML) to lead the transition to Industry 4.0, the possibilities are vast, especially at the edge. ABI Research predicts that by 2027, total camera system shipments will reach 197 million units and revenue will reach $35 billion. "The shift from machines capable of automating simple tasks to autonomous machines capable of 'seeing' elements for long-term optimization will drive new levels of industrial innovation. This is the innovation ML offers to MV (also known as computer vision)," ABIResear
