


'Focus on mature machine learning applications with investment value'
The Internet of Things (IoT) has grown steadily for more than a decade, driven by the proliferation of connected devices. Today's billions of connected devices provide businesses with unprecedented opportunities to collect and analyze data from the physical world to improve their business processes. In some cases, they are also driving novel and successful business models, leading enterprises to ride the wave of IoT adoption.
In most cases, enterprises process IoT data in edge clusters or clouds, not in edge devices and microcontrollers. The emergence of embedded machine learning and TinyML disrupts this paradigm, pushing application intelligence to the edge of the IoT network. As mentioned in the first article in this series, this provides significant benefits, including:
- Significant savings in bandwidth, energy, and storage resources
- Faster and low latency Opportunities to work with data
- Facilitate real-time control applications and drive timely decisions
- Leverage large amounts of data
The benefits are tangible and have clear business relevance . The ability for enterprises to use more data and processes at the edge of the network can increase business efficiency, which directly translates into monetary gains and improved corporate profits. Embedded machine learning is a game changer in artificial intelligence and IoT computing that can increase enterprise productivity. Here are 5 use cases for industrial enterprises deploying embedded machine learning.
INTELLIGENT ASSET MANAGEMENT AND INDUSTRIAL MAINTENANCE
Most industrial enterprises maintain assets based on a preventive maintenance approach, which depends on regular maintenance or replacement of machines and tools, etc. These intervals are determined by the maintenance policy provided by the equipment manufacturer. This approach helps avoid catastrophic production downtime events because assets are often maintained before failure occurs. However, preventive maintenance results in less than optimal asset utilization because assets are always replaced prematurely.
The emergence of Industry 4.0 and the Industrial Internet of Things enables industrial companies to implement condition-based monitoring of their assets. Leveraging digital data from sensors (e.g. vibration sensors, temperature sensors, thermal images) and asset management systems, businesses can now gain real-time visibility into the status of industrial assets such as tools and machinery. Additionally, using machine learning algorithms, they can gain predictive insights into the remaining useful life (RUL) of their assets. In some cases, reliable RUL estimates enable industrial companies to transform preventive maintenance into predictive maintenance. Predictive maintenance is the ultimate vision for maintenance and repair operations to achieve optimal Overall Equipment Effectiveness (OEE). Condition-based monitoring and predictive maintenance can help enterprises improve asset utilization, reduce production downtime, eliminate waste caused by equipment failure, and schedule maintenance tasks at the optimal time. Predictive maintenance is considered one of the killer applications of the fourth industrial revolution (Industry 4.0): it has a tangible return on investment and is applicable to almost all industrial sectors, including manufacturing, energy, construction, smart buildings, oil and gas, and mining, etc.
Most predictive maintenance deployments transmit and analyze data in the cloud. This approach has operational limitations, for example, failure predictions from cloud-based machine learning analytics are not always fast enough to take appropriate remedial or preventive actions. Embedded machine learning adds significant value to predictive maintenance and condition monitoring: it generates real-time insights and enables real-time decision-making. Performing machine learning directly on a data acquisition device or microcontroller inside the machine enables industrial companies to gain timely and accurate visibility into the status of various assets. This unlocks the potential for real-time decision-making based on actual equipment conditions. Overall, embedded machine learning improves the efficiency of predictive maintenance applications, increases asset utilization, and optimizes the quality of their services.
Quality Management and Zero-Defect Manufacturing
Machine learning has recently opened new horizons for quality management in manufacturing and production operations. Specifically, it gives the concept of predictive quality, that is, the ability to predict quality problems before they occur. In this regard, machine learning techniques, including deep learning, are applied to the production line. The purpose of its algorithms is to proactively identify conditions or patterns that lead to product defects. Based on this, the plant manager can take remedial measures to prevent defects from occurring. Additionally, machine learning techniques can be used to optimize patterns related to other parameters such as cost and environmental performance.
Embedded machine learning adds significant value to the quality management use cases mentioned above. Specifically, it provides a way to extract predictive insights into potential defects based on the processing of data inside a device. These insights can be combined with information from cloud analytics to identify process and control parameters that lead to quality issues. Likewise, they can be used to optimize multiple parameters simultaneously, enabling zero-defect manufacturing. Embedded machine learning thus provides factory managers and quality engineers with real-time asset-level information about defects, which complements existing knowledge about quality management issues. Therefore, it enables businesses to excel in implementing quality management strategies such as Total Quality Management (TQM) and Six Sigma. Overall, industrial companies can leverage embedded machine learning to supplement their existing quality management knowledge to improve product quality while reducing production time and costs.
Occupancy Monitoring in Facility Management
In recent years, the Internet of Things has had a transformative impact on smart building and facility management applications. Deploying sensors in buildings and other real estate assets allows property owners to access real-time, up-to-date information about the status of their properties. Based on this information, they can optimize the operation of HVAC (heating, ventilation and air conditioning) systems to save costs and improve their environmental indicators. In this regard, occupancy monitoring applications are very important.
Based on the processing of data from temperature and other sensors, an accurate understanding of the occupancy of rooms and other physical assets such as desks, computers and office spaces can be obtained. This is key to optimizing energy efficiency and maximizing tenant comfort. Additionally, it provides facility managers with real-time insights on asset utilization, allowing them to plan their usage and improve their overall productivity. Over the past few months, demand for such occupancy monitoring applications has surged due to the COVID-19 outbreak. The latter has led to the implementation of large-scale teleworking policies, which has made it more challenging for facilities managers to monitor and predict asset occupancy patterns. Sensors and IoT applications can help them by providing reliable and timely information about tenants’ physical presence in various spaces.
In facilities management environments, embedded machine learning improves the sustainability and accuracy of occupancy management applications. Specifically, it can run statistical data analysis within occupancy monitoring sensors without having to aggregate multiple sensor values through a cloud gateway. This improves the accuracy and timeliness of monitoring while also helping to reduce CO2 emissions. Embedded machine learning is important as facility managers are turning to IoT to reduce emissions and meet ambitious sustainability goals. In this way, they enhance their brand image and increase compliance with relevant regulations. For example, the recent New York City Climate Mobilization Act (CMA) requires buildings to be more energy efficient. Specifically, it mandates that buildings larger than 25,000 square feet must reduce greenhouse gas emissions by 40% by 2030 and by 80% by 2050, compared to 2005 levels. Overall, embedded machine learning is a powerful tool for next-generation energy-efficient facility management applications.
Cattle Monitoring
In the past few years, IoT systems and embedded devices have penetrated into the agricultural field and enabled precision farming. A prominent example is that sensors and ubiquitous connected devices such as beacons, RFID tags and specialized embedded sensors (such as stomach sensors) are increasingly being implanted in livestock to allow farmers to monitor them. To this end, relevant IoT applications tend to transmit raw data about the condition of cattle to the cloud for proper analysis. However, in some cases this approach may be inefficient or even unfeasible, as most cattle herds live in outdoor environments covering thousands of hectares in size. In this setting, network connectivity (e.g., short-range IoT networks) may not be sufficient to support the required quality of service during the data aggregation process. Furthermore, such devices often require battery power, which creates energy autonomy issues.
Embedded machine learning and TinyML provide substantial help in mitigating these limitations. Data analysis occurs on the livestock, which significantly reduces the amount of data that needs to be transferred to the application backend. Rather than collecting a continuous stream of data, deploying machine learning on embedded devices can stream data on a regular basis (e.g., every hour). This can provide farmers with insights into the condition of their animals and their activities (e.g., resting, suffering, or roaring). These insights enable farmers to make informed decisions about production processes such as milking and slaughtering. Overall, embedded machine learning helps farmers take advantage of precision livestock monitoring systems in situations where traditional cloud processing is impossible or ineffective.
Crisis Management
Machine learning and computational intelligence techniques are also used in crisis management and civil defense applications, including earthquake and wildfire predictions. In this regard, data from various sensors are often aggregated and processed in the cloud. However, in crisis management, time is of the essence: the success of crisis management actions largely depends on the timeliness of crisis management indicator predictions. For example, identifying earthquake warning signs earlier could lead to faster, more effective action. This is an area where embedded machine learning is of great value.
When it comes to wildfire management, embedded machine learning can provide reliability and deployment advantages, similar to cattle monitoring situations. In particular, executing statistical models within embedded sensors could facilitate timely predictions of wildfires without the need for strong network connections and battery-powered devices.
Summary
Embedded machine learning is widely used, and its application scope is not limited to the above five. For example, in precision agriculture, it can detect crop diseases directly on crops without the need for Various data streams are aggregated and analyzed in the cloud. Another example is that it enables precise refrigeration intelligence applications that directly analyze the temperature of sensitive products such as food, beverages and pharmaceuticals without having to use ambient temperature to estimate temperature anomalies. Overall, embedded machine learning unlocks nearly unlimited opportunities for innovation in many different areas.
However, developing and deploying embedded machine learning applications in industrial environments is not easy. Each implementation step must be carefully planned to meet stringent industrial requirements. From choosing the right embedded device to obtaining enough training data and implementing the right machine learning model, developers and deployers must make careful choices.
The above is the detailed content of 'Focus on mature machine learning applications with investment value'. For more information, please follow other related articles on the PHP Chinese website!

Hot AI Tools

Undresser.AI Undress
AI-powered app for creating realistic nude photos

AI Clothes Remover
Online AI tool for removing clothes from photos.

Undress AI Tool
Undress images for free

Clothoff.io
AI clothes remover

Video Face Swap
Swap faces in any video effortlessly with our completely free AI face swap tool!

Hot Article

Hot Tools

Notepad++7.3.1
Easy-to-use and free code editor

SublimeText3 Chinese version
Chinese version, very easy to use

Zend Studio 13.0.1
Powerful PHP integrated development environment

Dreamweaver CS6
Visual web development tools

SublimeText3 Mac version
God-level code editing software (SublimeText3)

Hot Topics


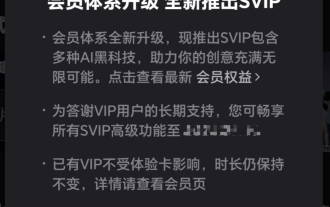
This site reported on June 27 that Jianying is a video editing software developed by FaceMeng Technology, a subsidiary of ByteDance. It relies on the Douyin platform and basically produces short video content for users of the platform. It is compatible with iOS, Android, and Windows. , MacOS and other operating systems. Jianying officially announced the upgrade of its membership system and launched a new SVIP, which includes a variety of AI black technologies, such as intelligent translation, intelligent highlighting, intelligent packaging, digital human synthesis, etc. In terms of price, the monthly fee for clipping SVIP is 79 yuan, the annual fee is 599 yuan (note on this site: equivalent to 49.9 yuan per month), the continuous monthly subscription is 59 yuan per month, and the continuous annual subscription is 499 yuan per year (equivalent to 41.6 yuan per month) . In addition, the cut official also stated that in order to improve the user experience, those who have subscribed to the original VIP
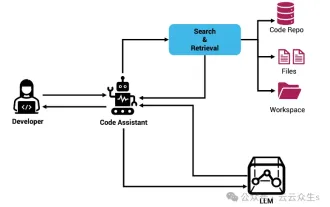
Improve developer productivity, efficiency, and accuracy by incorporating retrieval-enhanced generation and semantic memory into AI coding assistants. Translated from EnhancingAICodingAssistantswithContextUsingRAGandSEM-RAG, author JanakiramMSV. While basic AI programming assistants are naturally helpful, they often fail to provide the most relevant and correct code suggestions because they rely on a general understanding of the software language and the most common patterns of writing software. The code generated by these coding assistants is suitable for solving the problems they are responsible for solving, but often does not conform to the coding standards, conventions and styles of the individual teams. This often results in suggestions that need to be modified or refined in order for the code to be accepted into the application
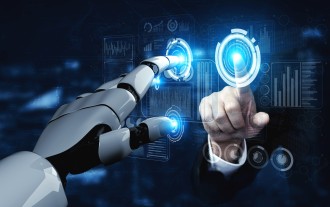
Large Language Models (LLMs) are trained on huge text databases, where they acquire large amounts of real-world knowledge. This knowledge is embedded into their parameters and can then be used when needed. The knowledge of these models is "reified" at the end of training. At the end of pre-training, the model actually stops learning. Align or fine-tune the model to learn how to leverage this knowledge and respond more naturally to user questions. But sometimes model knowledge is not enough, and although the model can access external content through RAG, it is considered beneficial to adapt the model to new domains through fine-tuning. This fine-tuning is performed using input from human annotators or other LLM creations, where the model encounters additional real-world knowledge and integrates it

To learn more about AIGC, please visit: 51CTOAI.x Community https://www.51cto.com/aigc/Translator|Jingyan Reviewer|Chonglou is different from the traditional question bank that can be seen everywhere on the Internet. These questions It requires thinking outside the box. Large Language Models (LLMs) are increasingly important in the fields of data science, generative artificial intelligence (GenAI), and artificial intelligence. These complex algorithms enhance human skills and drive efficiency and innovation in many industries, becoming the key for companies to remain competitive. LLM has a wide range of applications. It can be used in fields such as natural language processing, text generation, speech recognition and recommendation systems. By learning from large amounts of data, LLM is able to generate text
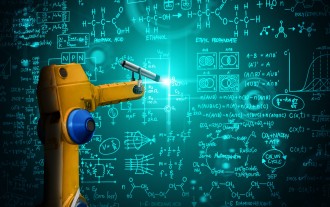
Machine learning is an important branch of artificial intelligence that gives computers the ability to learn from data and improve their capabilities without being explicitly programmed. Machine learning has a wide range of applications in various fields, from image recognition and natural language processing to recommendation systems and fraud detection, and it is changing the way we live. There are many different methods and theories in the field of machine learning, among which the five most influential methods are called the "Five Schools of Machine Learning". The five major schools are the symbolic school, the connectionist school, the evolutionary school, the Bayesian school and the analogy school. 1. Symbolism, also known as symbolism, emphasizes the use of symbols for logical reasoning and expression of knowledge. This school of thought believes that learning is a process of reverse deduction, through existing

Editor |ScienceAI Question Answering (QA) data set plays a vital role in promoting natural language processing (NLP) research. High-quality QA data sets can not only be used to fine-tune models, but also effectively evaluate the capabilities of large language models (LLM), especially the ability to understand and reason about scientific knowledge. Although there are currently many scientific QA data sets covering medicine, chemistry, biology and other fields, these data sets still have some shortcomings. First, the data form is relatively simple, most of which are multiple-choice questions. They are easy to evaluate, but limit the model's answer selection range and cannot fully test the model's ability to answer scientific questions. In contrast, open-ended Q&A
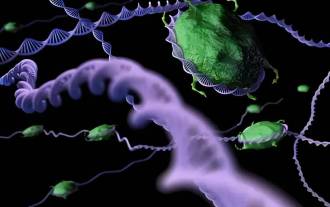
Editor | KX In the field of drug research and development, accurately and effectively predicting the binding affinity of proteins and ligands is crucial for drug screening and optimization. However, current studies do not take into account the important role of molecular surface information in protein-ligand interactions. Based on this, researchers from Xiamen University proposed a novel multi-modal feature extraction (MFE) framework, which for the first time combines information on protein surface, 3D structure and sequence, and uses a cross-attention mechanism to compare different modalities. feature alignment. Experimental results demonstrate that this method achieves state-of-the-art performance in predicting protein-ligand binding affinities. Furthermore, ablation studies demonstrate the effectiveness and necessity of protein surface information and multimodal feature alignment within this framework. Related research begins with "S
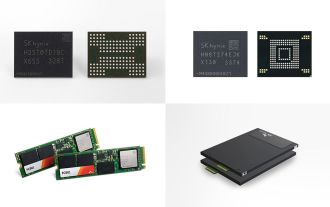
According to news from this site on August 1, SK Hynix released a blog post today (August 1), announcing that it will attend the Global Semiconductor Memory Summit FMS2024 to be held in Santa Clara, California, USA from August 6 to 8, showcasing many new technologies. generation product. Introduction to the Future Memory and Storage Summit (FutureMemoryandStorage), formerly the Flash Memory Summit (FlashMemorySummit) mainly for NAND suppliers, in the context of increasing attention to artificial intelligence technology, this year was renamed the Future Memory and Storage Summit (FutureMemoryandStorage) to invite DRAM and storage vendors and many more players. New product SK hynix launched last year
