


One person operates 4 robots, Han's collaborative robots help automate and flexibly ship welding
In the field of shipbuilding, welding is an extensive and crucial technology, and its quality directly affects the cycle, cost and quality of shipbuilding
In recent years, with the upward development of social economy, the younger generation has gradually "escaped" from high-intensity work (different welding point locations and types, operating postures of lying down, squatting, or lying down for a long time) and poor working environment (sultry, hot, The age structure of skilled welders in ship welding workshops where welding spatters and generally require wearing heavy protective clothing is abnormal, and the average age is significantly older. In addition, the high-end transformation of the domestic shipbuilding industry is accelerating, and companies have naturally higher and higher requirements for welding processes related to ship quality.
client needs
The customer is a "smart factory solution pilot demonstration" enterprise in the domestic shipping industry. It has built and delivered more than 270 high-quality ships to global users, including bulk carriers, car carriers, ultra-large container ships, oil tankers, and ore carriers. Special ships, dual-fuel ships, etc. have the reputation of "super cargo king at sea" in the industry.
The volume of shipbuilding welding depends on the ship type. Among the ship orders contracted by customers, medium and thick plates account for a relatively large proportion. In order to ensure quality, "each weld requires dozens of welding processes, and the pass rate during film inspection is required to reach 100%." Under such strict quality requirements, the efficiency of traditional manual welding cannot meet expectations. Customers hope to use more automated, flexible, and intelligent welding robots to achieve stable and reliable welding quality while improving welding efficiency and ensuring timely delivery. .
Hanzu Robot Solution:
Adopting the Elfin series collaborative robot body, it is light in weight and can be carried/carried to any location in the welding workshop by a single person; it is simple to operate, and can be quickly put into welding operations through drag-and-drop teaching or graphical programming; repeatable positioning accuracy Up to ±0.02mm, meeting welding accuracy requirements.
During actual welding operations, the welder master can easily complete welding task establishment, welding starting point, welding end point, welding start and other operations through the drag and drop process through the button at the end of the robotic arm, which is simple, convenient and efficient.
Compared with other collaborative robots, Han's Robot series products also have the following advantages, making them more suitable for welding applications:
The content that needs to be rewritten is: first, a robotic arm structure that is more suitable for welding. Han's robot adopts a unique double-joint module design. One motion module contains two joints, forming a unique kinematic structure, which can achieve higher flexibility during welding operations. The Elfin-Pro series of collaborative robots adopt internal circuit layout, and all welding operations can effectively avoid problems such as limited range of movement of the robotic arm and interference with communication signals due to entanglement of external wire harnesses
Second, more convenient and efficient teaching operation. Elfin-Pro supports integrated end force control, which can be easily dragged with only a drag force within 3N; it helps users drag the welding gun to the designated target solder point easily and quickly, achieving accuracy and improving work efficiency.
Third, it is more open and adaptable to all types of welding equipment. Han's robots can quickly adapt to domestic and foreign mainstream welding machines, including Megmeet, Rochi, Aotai, Binzer, Panasonic, Funis and Idaxin, etc., and can also cooperate with robot vision and control focusing on the welding industry. Efficient docking with device manufacturers to expand customers’ product selection space.
Adhering to the mission of “serving the people with robotic technology”, Han’s Robots continues to polish and optimize the welding process package to make welding operations simpler and more efficient. At the same time, Han's robots also have advantages in the field of welding such as "arc tracking", "laser visual seam tracking" and "multi-layer multi-pass welding".
effect evaluation:
Quality and efficiency are improved, saving manpower: According to the relevant person in charge of the customer's factory department, when all equipment is running normally, an ordinary welder can operate 4 welding robots at the same time, and the operating efficiency is greatly improved, and the welding quality is higher. Compared with traditional manual welding, it is more stable and reliable, and the consistency of the finished product is also stronger.
It is conducive to further improving the intelligence level of the welding workshop: strengthening the application of welding robots in the field of shipbuilding is an industry development trend. With the help of Han's Robots, the proportion of welding robots in customers' segmented production workshops has gradually increased, and the level of welding automation and intelligence has steadily improved, allowing customers to maintain a leading position in the increasingly competitive shipbuilding field.
Welding robots are closely integrated with ship construction and can significantly improve the production efficiency and automation level of shipbuilding and ship repair enterprises. Han's Robot will continue to explore the unique advantages of collaborative robots in ship welding and other fields, and provide users and partners with robotic arm products that are more suitable for welding
The above is the detailed content of One person operates 4 robots, Han's collaborative robots help automate and flexibly ship welding. For more information, please follow other related articles on the PHP Chinese website!

Hot AI Tools

Undresser.AI Undress
AI-powered app for creating realistic nude photos

AI Clothes Remover
Online AI tool for removing clothes from photos.

Undress AI Tool
Undress images for free

Clothoff.io
AI clothes remover

AI Hentai Generator
Generate AI Hentai for free.

Hot Article

Hot Tools

Notepad++7.3.1
Easy-to-use and free code editor

SublimeText3 Chinese version
Chinese version, very easy to use

Zend Studio 13.0.1
Powerful PHP integrated development environment

Dreamweaver CS6
Visual web development tools

SublimeText3 Mac version
God-level code editing software (SublimeText3)

Hot Topics


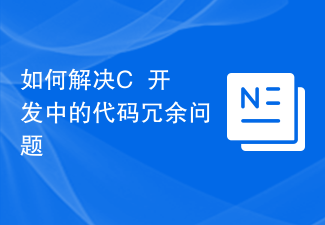
How to solve the code redundancy problem in C++ development. Code redundancy means that when writing a program, there are similar or repeated codes in multiple places. This problem not only makes the code difficult to maintain and read, but also increases the size and complexity of the code. For C++ developers, it is particularly important to solve the problem of code redundancy, because C++ is a powerful programming language, but it can also easily lead to code duplication. The root cause of code redundancy problems lies in unreasonable design and coding habits. To solve this problem, you can start from the following aspects: Use functions and classes: C
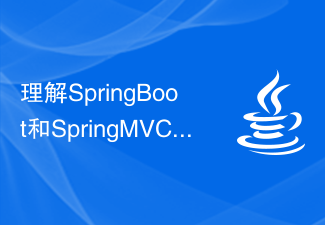
Compare SpringBoot and SpringMVC and understand their differences. With the continuous development of Java development, the Spring framework has become the first choice for many developers and enterprises. In the Spring ecosystem, SpringBoot and SpringMVC are two very important components. Although they are both based on the Spring framework, there are some differences in functions and usage. This article will focus on comparing SpringBoot and Spring
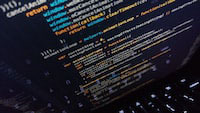
In modern software development, continuous integration (CI) has become an important practice to improve code quality and development efficiency. Among them, Jenkins is a mature and powerful open source CI tool, especially suitable for PHP applications. The following content will delve into how to use Jenkins to implement PHP continuous integration, and provide specific sample code and detailed steps. Jenkins installation and configuration First, Jenkins needs to be installed on the server. Just download and install the latest version from its official website. After the installation is complete, some basic configuration is required, including setting up an administrator account, plug-in installation, and job configuration. Create a new job On the Jenkins dashboard, click the "New Job" button. Select "Frees
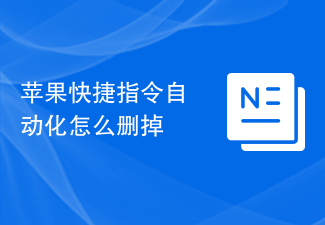
How to Delete Apple Shortcut Automation With the launch of Apple's new iOS13 system, users can use shortcuts (Apple Shortcuts) to customize and automate various mobile phone operations, which greatly improves the user's mobile phone experience. However, sometimes we may need to delete some shortcuts that are no longer needed. So, how to delete Apple shortcut command automation? Method 1: Delete through the Shortcuts app. On your iPhone or iPad, open the "Shortcuts" app. Select in the bottom navigation bar
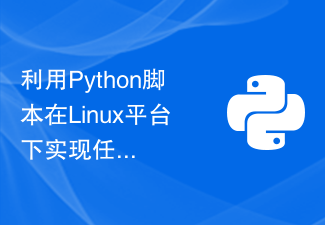
Using Python scripts to implement task scheduling and automation under the Linux platform In the modern information technology environment, task scheduling and automation have become essential tools for most enterprises. As a simple, easy-to-learn and feature-rich programming language, Python is very convenient and efficient to implement task scheduling and automation on the Linux platform. Python provides a variety of libraries for task scheduling, the most commonly used and powerful of which is crontab. crontab is a management and scheduling system

How to use Docker to realize automatic expansion and contraction of containers on Linux? Introduction: Containerization technology has become increasingly important and common in modern application development and deployment. As the leader in containerization technology, Docker provides a simple and powerful tool that can help developers quickly build, deploy and manage containerized applications. In this article, we will discuss how to use Docker to realize automatic expansion and contraction of containers in a Linux environment, and provide code examples to help readers better understand and practice
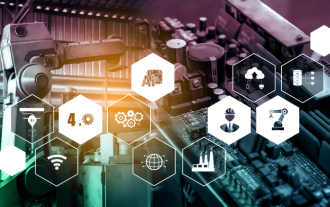
Automation technology is being widely used in different industries, especially in the supply chain field. Today, it has become an important part of supply chain management software. In the future, with the further development of automation technology, the entire supply chain and supply chain management software will undergo major changes. This will lead to more efficient logistics and inventory management, improve the speed and quality of production and delivery, and in turn promote the development and competitiveness of enterprises. Forward-thinking supply chain players are ready to deal with the new situation. CIOs should take the lead in ensuring the best outcomes for their organizations, and understanding the role of robotics, artificial intelligence, and automation in the supply chain is critical. What is supply chain automation? Supply chain automation refers to the use of technological means to reduce or eliminate human participation in supply chain activities. it covers a variety of
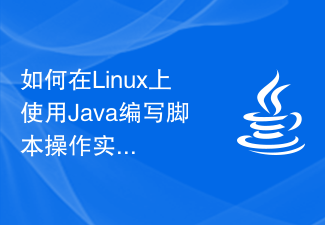
How to use Java to write scripts to automate operations on Linux In Linux systems, we can use Java to write scripts to automate operations. Java is a cross-platform programming language with powerful object-oriented features and rich class library support. In this article, we will learn how to use Java to write scripts to automate operations on Linux, and give specific code examples. First, we need to install the Java Development Kit (JDK) on Linux. I
