Help hotel uniform management system and related forms
Assist hotel uniform management system and related forms
Employee Work Clothes Management System
1. Purpose of work clothes management
In order to establish and maintain a good public image of the company and further standardize management, the following regulations have been formulated. We hope that everyone will comply with and strictly enforce these regulations.
2. Dressing and appearance during working hours
All employees must comply with the company's dress code to maintain a neat appearance and good mental state to project the company's professional image.
2. During working hours, we must pay attention to our appearance and dress neatly, appropriately and generously. This can leave a good impression.
3. Work clothes should be changed and washed frequently, and no buttons should be dropped, wrongly buttoned, or disconnected.
4. You must wear the work badge issued by the company during working hours.
3. Types of work clothes and usage time
Type of work clothes Season User Wearing time Ownership Remarks
Summer Clothes Winter Clothes
Work clothes 2 sets 2 sets All employees Working hours Employees Return after resignation
Reception service 2 sets 1 set Administrative and back-office staff Customer visit reception Company unified management
Season change time
Summer clothing: May 1st to October 31st
Winter clothing: November 1st to April 30th of the following year
4. Use and distribution of work clothes
1. Employees who have gone through formal entry procedures can receive work uniforms and work badges within three days of joining.
2. The distribution period of work uniforms is two years, and the distribution period of work badges is two years, starting from the date of distribution. If there is accidental damage due to work or other special circumstances and it needs to be replaced in advance, it must be filled in by myself. Please indicate the situation on the application form, and after verification by the Human Resources Department, early replacement will be granted.
3. If work clothes or work badges are lost, stolen, or damaged before expiration due to personal reasons, they must be replaced in advance and the corresponding fee (wholesale price) must be paid by the person.
4. When an employee resigns, the employee must return the work badge and work clothes together. At the same time, a certain fee will be charged for the work clothes received according to the following relevant regulations (deducted from the salary of the month of resignation):
(1) For those who leave less than half a year, 70% of the cost of work uniforms will be charged;
(2) For those who have resigned for more than half a year but less than one year, 50% of the cost of work uniforms will be charged.
5. Punishment measures
1. Employees who fail to wear work clothes as required will be punished with a penalty of 30 yuan/time in accordance with relevant company regulations;
2. If employees damage or lose their work clothes (improper washing and storage methods), they will be compensated twice as much as the production cost of the work clothes;
3. The employee's wearing of work clothes and appearance will be used as one of the basis for personal performance appraisal.
6. Compliance matters
1. During working hours, you must wear company uniforms and work badges issued by the company;
2. Employees are responsible for keeping and repairing the assigned work clothes;
3. The wear and tear of work clothes during non-working hours should be minimized;
4. Employees are not allowed to change the style of work clothes without authorization;
5. Employees are not allowed to lend work clothes without authorization;
6. Work clothes should be kept clean and tidy. If they are stained, employees should clean or repair them at their own expense;
7. The Human Resources Department is responsible for conducting irregular spot checks on the above behaviors. Those who do not dress according to regulations and wear work badges will be punished with a penalty of 30 yuan each time they are found, and will be included in the performance appraisal of the month;
8. Supervisors have the responsibility to guide and supervise employees in wearing work clothes.
Supplementary Provisions
The right to revise and interpret this system belongs to the Human Resources Department and will be promulgated after approval by the General Manager.
How to layout plaid clothes
Clothes layout is also called clothes layout. The method is as follows:
1. Necessary requirements for material placement
1. Order details
2. Full size size chart
3. Sample clothes or style pictures
Samples can be made from size charts and sample garments or style drawings
4. Fabric width and shrinkage (washing shrinkage, ironing shrinkage, etc., mainly washing shrinkage)
5. Other information - the quality of the fabric (mainly the color difference of the fabric), the characteristics of the fabric (whether it has directionality, such as the direction of the corduroy hair, the direction of the text pattern of the printed cloth, the yin and yang of the woven pattern) Texture conditions, etc.)
2. Select reasonable layout specifications and proportions based on the order details and size chart
1. The order details are proportional: it is relatively simple, but the proportional distribution situation must also be considered to reasonably select the layout specifications and proportional relationships.
2. If the order details are disproportionate: Reasonable methods must be used to select the layout specifications and proportional relationships (the principle is: use the least number of layouts to get the most accurate data - the purpose is to be convenient and quick)
3. If the jump values in the size table are consistent: Determine the overall selection specifications and proportional relationship (overall selection) according to the above two situations.
4. If the skip values in the size table are inconsistent: Put the skip values together to select the layout specifications and proportional relationship (segment selection).
5. There are several colors in the order details: if the specifications and quantities are the same, the layout specifications and proportions must be selected together according to the above method. If the specifications and quantities are different, the layout specifications and proportions must be selected separately (divided) color selection).
6. The above situations must be considered comprehensively (comprehensive selection).
3. Adopt reasonable layout methods based on the quality and characteristics of the fabric
1. Several situations of fabric quality:
(1) Segment gap - the same clothes should be gathered together as much as possible, and the length of the layout should be short rather than long
(2) Color difference in the edge - There are two cases of color difference in the edge: A. Side ——> Middle ——> Side; B. Side ——> Middle
The color difference in the edges should be combined with the characteristics of the style for reasonable arrangement. The principle is: the splicing parts should be put together or arranged on a meridional line. The appearance and main parts must ensure that the colors are naturally connected (some parts may not be possible) Avoid, such as the splicing of the collar of the top and the collar, the splicing of the back sleeve of the top and the back armhole, the inseam of the trousers, the splicing of the waist of the trousers and the trousers, etc.), the internal secondary parts can be flexible arrangement processing.
Usually when arranging five-pocket trousers with color difference in edge protection, the side seam can be placed on the edge of the door width or in the middle of the door width. However, if it is a pair of trousers with side leg pockets, the side seam must be placed It cannot be placed on the edge of the door width, otherwise the side pockets will not be well placed.
(3) There is both step difference and edge color difference - usually the color difference that is more obvious or serious is judged by appearance as the main control object. If it is serious, the fabric used can be judged as unusable fabric, that is, as Disposal of non-conforming products.
2. Disposal method based on the characteristics of the fabric:
(1) Conventional fabrics have no directionality, so any arrangement method that saves fabrics is adopted;
(2) If the fabric has directionality, it should be treated separately according to the situation. If the fabric has a hair direction, it should be considered whether it is completely down or smooth, or it can be one direction per piece; if the fabric has a printing pattern direction, it should be based on the customer's requirements. Unify the direction (especially be careful if the plaid fabric has a yin and yang pattern); if the woven pattern has a yin and yang effect, consider one piece in one direction or operate according to the customer's requirements.
(3) If the fabric is directional and has color difference (mainly focusing on the color difference in the edges), the layout principle is to minimize the parts with color difference (such as corduroy scratch-dyed fabrics or directional printed fabrics). For style trousers, place four trousers pieces on top of a door width. If the door width is not wide enough to place four pieces, you can stagger them up and down to keep the splicing parts on the same line, so that the most likely areas of color difference will appear. It is the back wave area and the inner crotch area. If other methods are adopted, the color difference may occur in more than these two areas).
3. To control the layout length:
Generally, the length of the pattern is controlled at about 8 meters, and it is best not to exceed 9 meters, because the length of the cutting table in the factory is usually 10 meters, and the length is controlled at about 8 meters to facilitate the actual operation of the factory; in addition, we usually have single tops The consumption is about 2 meters, and the single consumption of pants is about 1.4 meters. Generally, the total length of a 4-piece row of tops and a 6-piece row of trousers is about 8 meters. For fabrics with step differences, the length should be shortened as much as possible. For fabrics with striped styles, the length should not be too long. Knitted fabrics are affected by the elasticity of the fabric and should not be too long. Those with relatively high elasticity should not be too long and are easily deformed. The length of the fabric should not be too long.
Relatively speaking, a longer version can save the loss of knife edge material but increase the amount of scraps. A shorter version will increase the loss of knife edge material and reduce the amount of scraps. The specific operation requires comprehensive judgment to choose a reasonable one. Way.
The above is the detailed content of Help hotel uniform management system and related forms. For more information, please follow other related articles on the PHP Chinese website!

Hot AI Tools

Undresser.AI Undress
AI-powered app for creating realistic nude photos

AI Clothes Remover
Online AI tool for removing clothes from photos.

Undress AI Tool
Undress images for free

Clothoff.io
AI clothes remover

AI Hentai Generator
Generate AI Hentai for free.

Hot Article

Hot Tools

Notepad++7.3.1
Easy-to-use and free code editor

SublimeText3 Chinese version
Chinese version, very easy to use

Zend Studio 13.0.1
Powerful PHP integrated development environment

Dreamweaver CS6
Visual web development tools

SublimeText3 Mac version
God-level code editing software (SublimeText3)

Hot Topics


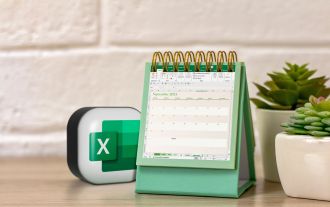
Excel web version features enhancements to improve efficiency! While Excel desktop version is more powerful, the web version has also been significantly improved over the past year. This article will focus on five key improvements: Easily insert rows and columns: In Excel web, just hover over the row or column header and click the " " sign that appears to insert a new row or column. There is no need to use the confusing right-click menu "insert" function anymore. This method is faster, and newly inserted rows or columns inherit the format of adjacent cells. Export as CSV files: Excel now supports exporting worksheets as CSV files for easy data transfer and compatibility with other software. Click "File" > "Export"
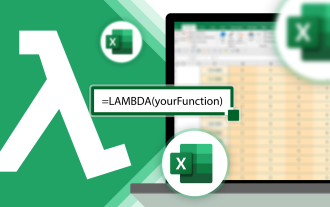
Excel's LAMBDA Functions: An easy guide to creating custom functions Before Excel introduced the LAMBDA function, creating a custom function requires VBA or macro. Now, with LAMBDA, you can easily implement it using the familiar Excel syntax. This guide will guide you step by step how to use the LAMBDA function. It is recommended that you read the parts of this guide in order, first understand the grammar and simple examples, and then learn practical applications. The LAMBDA function is available for Microsoft 365 (Windows and Mac), Excel 2024 (Windows and Mac), and Excel for the web. E
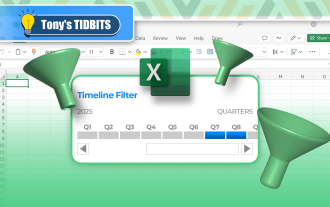
In Excel, using the timeline filter can display data by time period more efficiently, which is more convenient than using the filter button. The Timeline is a dynamic filtering option that allows you to quickly display data for a single date, month, quarter, or year. Step 1: Convert data to pivot table First, convert the original Excel data into a pivot table. Select any cell in the data table (formatted or not) and click PivotTable on the Insert tab of the ribbon. Related: How to Create Pivot Tables in Microsoft Excel Don't be intimidated by the pivot table! We will teach you basic skills that you can master in minutes. Related Articles In the dialog box, make sure the entire data range is selected (
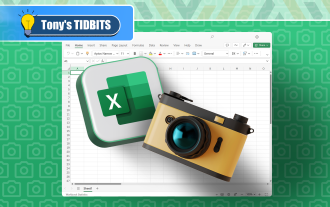
Quick Links Why Use the Camera Tool?
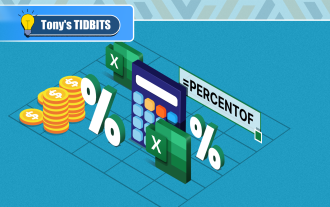
Excel's PERCENTOF function: Easily calculate the proportion of data subsets Excel's PERCENTOF function can quickly calculate the proportion of data subsets in the entire data set, avoiding the hassle of creating complex formulas. PERCENTOF function syntax The PERCENTOF function has two parameters: =PERCENTOF(a,b) in: a (required) is a subset of data that forms part of the entire data set; b (required) is the entire dataset. In other words, the PERCENTOF function calculates the percentage of the subset a to the total dataset b. Calculate the proportion of individual values using PERCENTOF The easiest way to use the PERCENTOF function is to calculate the single
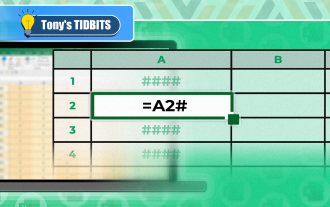
Excel Overflow Range Operator (#) enables formulas to be automatically adjusted to accommodate changes in overflow range size. This feature is only available for Microsoft 365 Excel for Windows or Mac. Common functions such as UNIQUE, COUNTIF, and SORTBY can be used in conjunction with overflow range operators to generate dynamic sortable lists. The pound sign (#) in the Excel formula is also called the overflow range operator, which instructs the program to consider all results in the overflow range. Therefore, even if the overflow range increases or decreases, the formula containing # will automatically reflect this change. How to list and sort unique values in Microsoft Excel
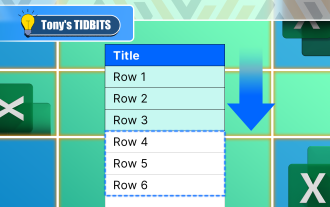
Use formula conditional formatting to handle overflow arrays in Excel Direct formatting of overflow arrays in Excel can cause problems, especially when the data shape or size changes. Formula-based conditional formatting rules allow automatic formatting to be adjusted when data parameters change. Adding a dollar sign ($) before a column reference applies a rule to all rows in the data. In Excel, you can apply direct formatting to the values or background of a cell to make the spreadsheet easier to read. However, when an Excel formula returns a set of values (called overflow arrays), applying direct formatting will cause problems if the size or shape of the data changes. Suppose you have this spreadsheet with overflow results from the PIVOTBY formula,
