How to create maximum business value through process optimization
By improving key processes, businesses can save millions of dollars every year, not only improve cash flow, but also provide many other benefits, such as improved compliance, Enhance interactions with customers, employees, candidates, and more. However, it is important to note that with process optimization across complex corporate systems, it is easy to run into difficulties that may cause the optimization plan to stall or not fully realize its value.
By following the most effective steps for actionable process transformation, businesses can get the best results from their process optimization efforts.
Adhering to best practices is especially critical for organizations planning to leverage artificial intelligence and automation to optimize processes. While AI-driven automation can streamline processes, the same technology can cause problems to become more complex if the solution is poorly designed or deployed without planning and execution. Therefore, it is critical to ensure that process requirements are fully understood throughout the implementation process, and to work closely with relevant stakeholders. In addition, continuous monitoring and evaluation of the performance of AI systems, and timely adjustments and improvements are also important to ensure the efficient operation of automated processes. Ultimately, continuous learning and adapting to new technologies and best practices are the three core challenges of process optimization. Many companies have been working on improving their processes for years, but it is difficult to achieve their ambitious goals. Challenges are often faced for three root causes:
Complexity:Within an enterprise, processes are horizontal, often across multiple departments and systems - each with own priorities, needs, culture and established ways of doing things, this level of complexity makes it difficult to know where to start optimizing and how to do it in a way that works for different stakeholders and benefits the entire enterprise.
Lack of transparency: With respect to the process itself, complexity and silos can make it difficult to collect data and conduct end-to-end analysis. The more complex and opaque the process, the harder it is to These goals are linked to strategic business goals.
Subjectivity: Too often we see decisions about process improvements being based on intuition and partial or outdated analysis, rather than analyzing data that reflects the current state.
These barriers often occur simultaneously and can prevent businesses from successfully leveraging process optimization to achieve maximum ROI. Follow an optimization strategy to maximize value
We’ve found the following best practices to be the most helpful in achieving business goals and creating lasting improvements:
Will you Decisions focus on the value to be delivered. Successful companies establish dedicated governance with the right roles, working methods, tools and decision-making structures to drive business value. For companies in the early stages of their journey, demonstrate the value of these efforts (usually measured by ROI) in one or two priority areas.- Build a team dedicated to this work and embed it into the company’s ongoing operations.
- A value-centered mindset starts with choosing the right problem to solve and considering what success will look like once the problem is solved. Will employees be more productive? Or will there be significant cost savings by eliminating excess inventory or reducing services obtained from third parties? Some efforts may even lead to additional revenue or cash flow improvements.
-
Expectations for a successful improvement process help prioritize and sequence the multiple use cases under consideration. It also helps justify the allocation of capacity among the teams that must come together to deliver the work. Ultimately, It clarifies who in the business needs approval and recognizes the value of getting it done.
By following this guidance, early adopters are more likely to select use cases that generate significant ROI, guiding the enterprise to invest in continuing the process improvement journey.
Setting the Scope of a Process Optimization Project
Process optimization efforts can deliver significant value in many areas of a business, and while some areas such as finance and procurement are already well understood, others are starting to Get more attention.
Specifically, we see companies across all industries developing many innovative solutions:
- Real-time supply chain planning
- INTELLIGENT MANUFACTURING FACTORY
- Engineering Design Management
- Redesign HR to improve experience and efficiency
- Simplify Master Data Management
There are no processes that can be handled by this method Limitations - The only requirements include:
- Get accurate data.
- Contributions from process owners and/or experts to generate analysis and insights.
- Processes with a large number of activities and a large number of associated costs.
For example, a consumer goods manufacturer that recently used process improvements to avoid food waste and reduce costs had finished goods in its warehouses past the date they could be sold to end customers, the company used data to highlight situations where planned production is out of sync with current demand. For products that are nearing their end date, the AI solution suggests a number of next-best actions—from moving to other warehouses with higher demand, selling at a discount, or ultimately donating.
Another organization, a retailer, used innovative technology and data insights to improve the effectiveness of its supply chain planning process. Initially, supply chain planners used several different systems to gather information about product demand, Information on supply schedules and supplier orders. Process mining techniques allow this information to be integrated into a knowledge model – reducing the effort of extracting information from disparate systems and helping to interpret content. This allows planning delays and supply risks to be discovered in near real-time, so planners can take immediate action, Avoid impact.
Make process optimization part of the organizational fabric
After demonstrating early success, companies often hit the next big challenge in their journey, which is how to adopt enterprise-wide adoption This method. The ultimate goal is to embed this into the company's ongoing operations and management so that these efforts evolve from projects to business-as-usual activities. To achieve this enterprise-wide, organizations must consider the following:
- Governance and funding mechanisms: Ensure business and IT leadership are involved and make decisions together to guide the effort.
- Center of Excellence: Achieve rapid expansion and sharing of knowledge and capabilities.
- Technology Stack Selection, Implementation, and Update: Identify the most important tools and technologies that will help solve the most pressing problems.
- Value realization and measurement: Use value thinking to drive the identification, prioritization and execution of work.
Process optimization that delivers the greatest value doesn’t start with a specific technology in mind, rather it’s about taking the right approach to assess the efficiency of your processes, develop smarter ways of working, and Introduce automation and other technologies where they add measurable value.
Process optimization should be continuous. This is because as you improve your processes, your organization will discover new problems and identify new ways to solve them. Keep these learnings in a centralized process center of excellence to support the future. process improvements.
Supported by effective governance and targeted funding mechanisms, accelerated and continuous process improvement can become part of the organizational culture, making process optimization easier to implement and achieve a greater return on effort.
The above is the detailed content of How to create maximum business value through process optimization. For more information, please follow other related articles on the PHP Chinese website!

Hot AI Tools

Undresser.AI Undress
AI-powered app for creating realistic nude photos

AI Clothes Remover
Online AI tool for removing clothes from photos.

Undress AI Tool
Undress images for free

Clothoff.io
AI clothes remover

AI Hentai Generator
Generate AI Hentai for free.

Hot Article

Hot Tools

Notepad++7.3.1
Easy-to-use and free code editor

SublimeText3 Chinese version
Chinese version, very easy to use

Zend Studio 13.0.1
Powerful PHP integrated development environment

Dreamweaver CS6
Visual web development tools

SublimeText3 Mac version
God-level code editing software (SublimeText3)

Hot Topics
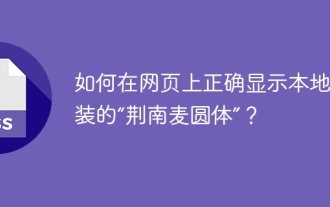
Using locally installed font files in web pages Recently, I downloaded a free font from the internet and successfully installed it into my system. Now...

The main sources of H5 page materials are: 1. Professional material website (paid, high quality, clear copyright); 2. Homemade material (high uniqueness, but time-consuming); 3. Open source material library (free, need to be carefully screened); 4. Picture/video website (copyright verified is required). In addition, unified material style, size adaptation, compression processing, and copyright protection are key points that need to be paid attention to.
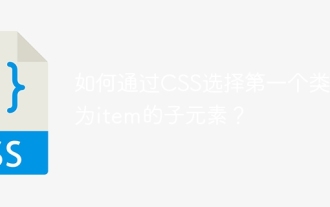
When the number of elements is not fixed, how to select the first child element of the specified class name through CSS. When processing HTML structure, you often encounter different elements...
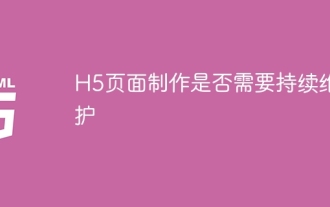
The H5 page needs to be maintained continuously, because of factors such as code vulnerabilities, browser compatibility, performance optimization, security updates and user experience improvements. Effective maintenance methods include establishing a complete testing system, using version control tools, regularly monitoring page performance, collecting user feedback and formulating maintenance plans.
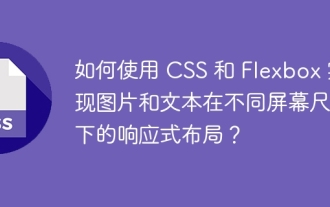
Implementing responsive layouts using CSS When we want to implement layout changes under different screen sizes in web design, CSS...
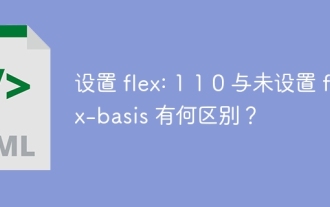
The difference between flex:110 in Flex layout and flex-basis not set In Flex layout, how to set flex...
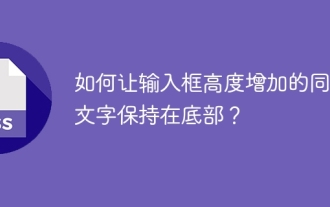
How to keep the text at the bottom while the input box height increases? During the development process, we often encounter the need to adjust the input box height, and at the same time hope...
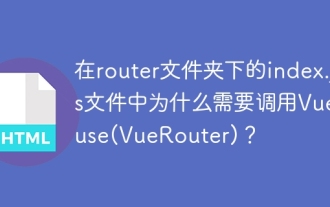
The necessity of registering VueRouter in the index.js file under the router folder When developing Vue applications, you often encounter problems with routing configuration. Special...
