


Utiliser l'IA pour corriger les erreurs de fabrication additive en temps réel
Des chercheurs du Massachusetts Institute of Technology (MIT) ont formé un modèle d'apprentissage automatique pour surveiller et ajuster le processus d'impression 3D afin de corriger les erreurs en temps réel.
De nouveaux matériaux pouvant être utilisés pour l'impression 3D sont constamment développés, mais savoir comment imprimer avec eux peut être un casse-tête complexe et coûteux. En règle générale, les opérateurs doivent recourir à des essais et des erreurs manuels, exécutant potentiellement des milliers d'impressions, pour déterminer les paramètres idéaux pour imprimer de nouveaux matériaux de manière cohérente et efficace.
Des chercheurs du MIT ont utilisé l'intelligence artificielle pour rationaliser le processus. Les scientifiques de l'agence ont développé un nouveau système d'apprentissage automatique qui utilise la vision par ordinateur pour observer le processus de fabrication et peut corriger les erreurs dans la façon dont les matériaux sont manipulés en temps réel.
Ils ont utilisé la simulation pour apprendre à un réseau neuronal comment ajuster les paramètres d'impression afin de minimiser les erreurs, puis ont appliqué ce contrôleur à une véritable imprimante 3D. Le nouveau système peut imprimer des objets avec plus de précision que les autres contrôleurs d'impression 3D existants.
Ce travail évite le processus coûteux d'impression de milliers ou de millions d'objets réels pour entraîner les réseaux de neurones. Cela pourrait permettre aux ingénieurs d’intégrer plus facilement de nouveaux matériaux dans leurs produits imprimés en 3D, ce qui pourrait les aider à développer des produits dotés de propriétés électriques ou chimiques particulières. Cela aide également les techniciens à apporter des ajustements au processus d'impression lorsque les matériaux ou les conditions environnementales changent de manière inattendue.
"Ce projet est vraiment la première démonstration de la construction d'un système de fabrication qui utilise l'apprentissage automatique pour apprendre des stratégies de contrôle complexes", a déclaré Wojciech Matusik, professeur de génie électrique et d'informatique au MIT qui dirige le projet. plus d'équipements de fabrication intelligents qui peuvent s'adapter en temps réel à l'environnement changeant du lieu de travail pour augmenter le rendement ou la précision du système, vous pourrez alors tirer plus de valeur de vos machines "
Choisir les paramètres
OK. Déterminer les paramètres idéaux car un processus de fabrication numérique peut être l’une des parties les plus coûteuses du processus, car il nécessite de nombreux essais et erreurs. Une fois que le technicien a trouvé une combinaison qui fonctionne bien, ces paramètres ne s'appliquent qu'à une situation précise. Ils disposent de peu de données sur le comportement du matériau dans d’autres environnements, sur un matériel différent ou dans de nouveaux lots, présentant des propriétés différentes.
L'utilisation de systèmes d'apprentissage automatique est également pleine de défis. Premièrement, les chercheurs doivent mesurer en temps réel ce qui se passe sur l’imprimante 3D.
Pour ce faire, les chercheurs ont développé un système de vision industrielle utilisant deux caméras pointées vers la buse de l’imprimante 3D. Le système éclaire le matériau au fur et à mesure de son dépôt et calcule l'épaisseur du matériau en fonction de la quantité de lumière qui le traverse. "Vous pouvez considérer le système visuel comme une paire d'yeux observant ce processus en temps réel", a déclaré Foshey.
Le contrôleur traitera ensuite les images qu'il reçoit du système de vision et ajustera la vitesse d'alimentation et l'orientation de l'imprimante en fonction des erreurs qu'il détecte.
Cependant, former un contrôleur basé sur un réseau neuronal pour comprendre ce processus de fabrication nécessite de nombreuses données et des millions d'impressions. Les chercheurs ont donc construit un simulateur.
Simulation réussie
Pour mieux entraîner le contrôleur, ils ont utilisé un processus appelé apprentissage par renforcement, dans lequel le modèle apprend par essais et erreurs et est récompensé. La tâche du modèle est de sélectionner les paramètres d'impression afin de créer des objets spécifiques dans l'environnement de simulation. Après avoir affiché le résultat attendu, le modèle est récompensé lorsqu'il sélectionne des paramètres qui minimisent l'erreur entre son impression et le résultat attendu.
Dans ce cas, « erreur » signifie que le modèle soit alloue trop de matière, le laissant dans des zones qui devraient rester ouvertes, soit il n'alloue pas assez de matière, laissant des endroits ouverts qui devraient être remplis. Au fur et à mesure que le modèle effectue davantage d'impressions simulées, il met à jour sa stratégie de contrôle pour maximiser les récompenses, devenant de plus en plus précise.
Cependant, le monde réel est plus compliqué que la simulation. Dans la pratique, les conditions varient souvent en raison de petits changements ou du bruit dans le processus d'impression. Les chercheurs ont donc créé un modèle numérique qui se rapproche du bruit d’une imprimante 3D. Ils ont utilisé ce modèle pour ajouter du bruit à leurs simulations, produisant ainsi des résultats plus réalistes.
"Ce que nous avons trouvé intéressant, c'est qu'en implémentant ce modèle de bruit, nous avons pu transférer des stratégies de contrôle formées uniquement en simulation vers du matériel sans aucune formation en expériences physiques", a déclaré Foshey, "Et ensuite, nous n'avons pas eu besoin de peaufiner l'appareil lui-même. »
Lorsque le contrôleur a été testé, il a imprimé les objets avec plus de précision que toute autre méthode de contrôle précédemment évaluée. Il fonctionne particulièrement bien dans l’impression intercalaire, qui consiste à imprimer l’intérieur d’un objet. Certains autres contrôleurs ont déposé tellement de matière que les objets imprimés ont été soulevés, mais le contrôleur des chercheurs a ajusté le chemin d'impression pour que les objets restent de niveau.
Leur stratégie de contrôle peut même comprendre comment le matériau se propage après le dépôt et ajuster les paramètres en conséquence.
Ajustement automatique
"Nous sommes également en mesure de concevoir des stratégies de contrôle permettant de contrôler dynamiquement différents types de matériaux. Ainsi, si vous avez un processus de fabrication sur site et que vous souhaitez changer de matériaux, vous n'avez pas besoin de revalider le processus de fabrication. Vous pouvez simplement chargez le nouveau matériau dans le contrôleur. Il s'ajustera automatiquement", a déclaré Foshey.
Maintenant qu'ils ont démontré l'efficacité de cette technique pour l'impression 3D, les chercheurs espèrent développer des contrôleurs pour d'autres procédés de fabrication. Ils souhaitent également voir comment la méthode peut être modifiée pour gérer plusieurs couches de matériaux ou imprimer plusieurs matériaux en même temps. De plus, leur méthode suppose que chaque matériau a une viscosité fixe, mais les futures itérations pourraient utiliser l’IA pour identifier et ajuster la viscosité en temps réel.
MIT a une longue histoire dans la fabrication additive et a donné naissance à plusieurs grandes sociétés d'impression 3D, telles que Desktop Metal et VulcanForms. Ce travail a été soutenu en partie par le programme FWF Lise-Meitner, une subvention de démarrage du Conseil européen de la recherche et la National Science Foundation.
Ce qui précède est le contenu détaillé de. pour plus d'informations, suivez d'autres articles connexes sur le site Web de PHP en chinois!

Outils d'IA chauds

Undresser.AI Undress
Application basée sur l'IA pour créer des photos de nu réalistes

AI Clothes Remover
Outil d'IA en ligne pour supprimer les vêtements des photos.

Undress AI Tool
Images de déshabillage gratuites

Clothoff.io
Dissolvant de vêtements AI

AI Hentai Generator
Générez AI Hentai gratuitement.

Article chaud

Outils chauds

Bloc-notes++7.3.1
Éditeur de code facile à utiliser et gratuit

SublimeText3 version chinoise
Version chinoise, très simple à utiliser

Envoyer Studio 13.0.1
Puissant environnement de développement intégré PHP

Dreamweaver CS6
Outils de développement Web visuel

SublimeText3 version Mac
Logiciel d'édition de code au niveau de Dieu (SublimeText3)
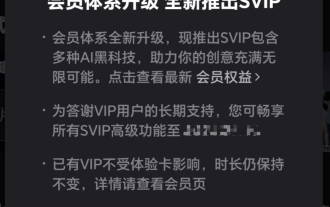
Ce site a rapporté le 27 juin que Jianying est un logiciel de montage vidéo développé par FaceMeng Technology, une filiale de ByteDance. Il s'appuie sur la plateforme Douyin et produit essentiellement du contenu vidéo court pour les utilisateurs de la plateforme. Il est compatible avec iOS, Android et. Windows, MacOS et autres systèmes d'exploitation. Jianying a officiellement annoncé la mise à niveau de son système d'adhésion et a lancé un nouveau SVIP, qui comprend une variété de technologies noires d'IA, telles que la traduction intelligente, la mise en évidence intelligente, l'emballage intelligent, la synthèse humaine numérique, etc. En termes de prix, les frais mensuels pour le clipping SVIP sont de 79 yuans, les frais annuels sont de 599 yuans (attention sur ce site : équivalent à 49,9 yuans par mois), l'abonnement mensuel continu est de 59 yuans par mois et l'abonnement annuel continu est de 59 yuans par mois. est de 499 yuans par an (équivalent à 41,6 yuans par mois) . En outre, le responsable de Cut a également déclaré que afin d'améliorer l'expérience utilisateur, ceux qui se sont abonnés au VIP d'origine
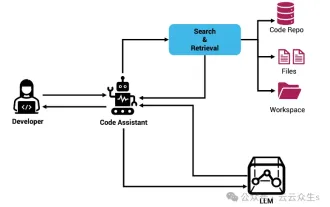
Améliorez la productivité, l’efficacité et la précision des développeurs en intégrant une génération et une mémoire sémantique améliorées par la récupération dans les assistants de codage IA. Traduit de EnhancingAICodingAssistantswithContextUsingRAGandSEM-RAG, auteur JanakiramMSV. Bien que les assistants de programmation d'IA de base soient naturellement utiles, ils ne parviennent souvent pas à fournir les suggestions de code les plus pertinentes et les plus correctes, car ils s'appuient sur une compréhension générale du langage logiciel et des modèles d'écriture de logiciels les plus courants. Le code généré par ces assistants de codage est adapté à la résolution des problèmes qu’ils sont chargés de résoudre, mais n’est souvent pas conforme aux normes, conventions et styles de codage des équipes individuelles. Cela aboutit souvent à des suggestions qui doivent être modifiées ou affinées pour que le code soit accepté dans l'application.
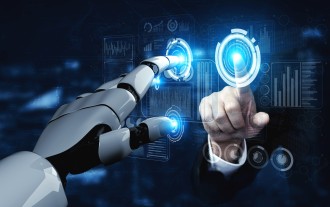
Les grands modèles linguistiques (LLM) sont formés sur d'énormes bases de données textuelles, où ils acquièrent de grandes quantités de connaissances du monde réel. Ces connaissances sont intégrées à leurs paramètres et peuvent ensuite être utilisées en cas de besoin. La connaissance de ces modèles est « réifiée » en fin de formation. À la fin de la pré-formation, le modèle arrête effectivement d’apprendre. Alignez ou affinez le modèle pour apprendre à exploiter ces connaissances et répondre plus naturellement aux questions des utilisateurs. Mais parfois, la connaissance du modèle ne suffit pas, et bien que le modèle puisse accéder à du contenu externe via RAG, il est considéré comme bénéfique de l'adapter à de nouveaux domaines grâce à un réglage fin. Ce réglage fin est effectué à l'aide de la contribution d'annotateurs humains ou d'autres créations LLM, où le modèle rencontre des connaissances supplémentaires du monde réel et les intègre.

Pour en savoir plus sur l'AIGC, veuillez visiter : 51CTOAI.x Community https://www.51cto.com/aigc/Translator|Jingyan Reviewer|Chonglou est différent de la banque de questions traditionnelle que l'on peut voir partout sur Internet. nécessite de sortir des sentiers battus. Les grands modèles linguistiques (LLM) sont de plus en plus importants dans les domaines de la science des données, de l'intelligence artificielle générative (GenAI) et de l'intelligence artificielle. Ces algorithmes complexes améliorent les compétences humaines et stimulent l’efficacité et l’innovation dans de nombreux secteurs, devenant ainsi la clé permettant aux entreprises de rester compétitives. LLM a un large éventail d'applications. Il peut être utilisé dans des domaines tels que le traitement du langage naturel, la génération de texte, la reconnaissance vocale et les systèmes de recommandation. En apprenant de grandes quantités de données, LLM est capable de générer du texte

L'ensemble de données ScienceAI Question Answering (QA) joue un rôle essentiel dans la promotion de la recherche sur le traitement du langage naturel (NLP). Des ensembles de données d'assurance qualité de haute qualité peuvent non seulement être utilisés pour affiner les modèles, mais également évaluer efficacement les capacités des grands modèles linguistiques (LLM), en particulier la capacité à comprendre et à raisonner sur les connaissances scientifiques. Bien qu’il existe actuellement de nombreux ensembles de données scientifiques d’assurance qualité couvrant la médecine, la chimie, la biologie et d’autres domaines, ces ensembles de données présentent encore certaines lacunes. Premièrement, le formulaire de données est relativement simple, et la plupart sont des questions à choix multiples. Elles sont faciles à évaluer, mais limitent la plage de sélection des réponses du modèle et ne peuvent pas tester pleinement la capacité du modèle à répondre aux questions scientifiques. En revanche, les questions et réponses ouvertes
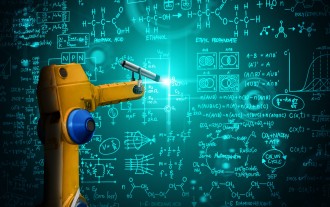
L'apprentissage automatique est une branche importante de l'intelligence artificielle qui donne aux ordinateurs la possibilité d'apprendre à partir de données et d'améliorer leurs capacités sans être explicitement programmés. L'apprentissage automatique a un large éventail d'applications dans divers domaines, de la reconnaissance d'images et du traitement du langage naturel aux systèmes de recommandation et à la détection des fraudes, et il change notre façon de vivre. Il existe de nombreuses méthodes et théories différentes dans le domaine de l'apprentissage automatique, parmi lesquelles les cinq méthodes les plus influentes sont appelées les « Cinq écoles d'apprentissage automatique ». Les cinq grandes écoles sont l’école symbolique, l’école connexionniste, l’école évolutionniste, l’école bayésienne et l’école analogique. 1. Le symbolisme, également connu sous le nom de symbolisme, met l'accent sur l'utilisation de symboles pour le raisonnement logique et l'expression des connaissances. Cette école de pensée estime que l'apprentissage est un processus de déduction inversée, à travers les connaissances existantes.
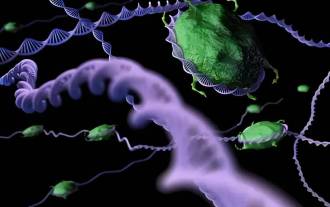
Editeur | KX Dans le domaine de la recherche et du développement de médicaments, il est crucial de prédire avec précision et efficacité l'affinité de liaison des protéines et des ligands pour le criblage et l'optimisation des médicaments. Cependant, les études actuelles ne prennent pas en compte le rôle important des informations sur la surface moléculaire dans les interactions protéine-ligand. Sur cette base, des chercheurs de l'Université de Xiamen ont proposé un nouveau cadre d'extraction de caractéristiques multimodales (MFE), qui combine pour la première fois des informations sur la surface des protéines, la structure et la séquence 3D, et utilise un mécanisme d'attention croisée pour comparer différentes modalités. alignement. Les résultats expérimentaux démontrent que cette méthode atteint des performances de pointe dans la prédiction des affinités de liaison protéine-ligand. De plus, les études d’ablation démontrent l’efficacité et la nécessité des informations sur la surface des protéines et de l’alignement des caractéristiques multimodales dans ce cadre. Les recherches connexes commencent par "S
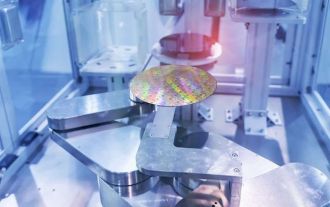
Selon les informations de ce site Web du 5 juillet, GlobalFoundries a publié un communiqué de presse le 1er juillet de cette année, annonçant l'acquisition de la technologie de nitrure de gallium (GaN) et du portefeuille de propriété intellectuelle de Tagore Technology, dans l'espoir d'élargir sa part de marché dans l'automobile et Internet. des objets et des domaines d'application des centres de données d'intelligence artificielle pour explorer une efficacité plus élevée et de meilleures performances. Alors que des technologies telles que l’intelligence artificielle générative (GenerativeAI) continuent de se développer dans le monde numérique, le nitrure de gallium (GaN) est devenu une solution clé pour une gestion durable et efficace de l’énergie, notamment dans les centres de données. Ce site Web citait l'annonce officielle selon laquelle, lors de cette acquisition, l'équipe d'ingénierie de Tagore Technology rejoindrait GF pour développer davantage la technologie du nitrure de gallium. g
